How a CMMS Drives Time and Cost Savings for FM Teams
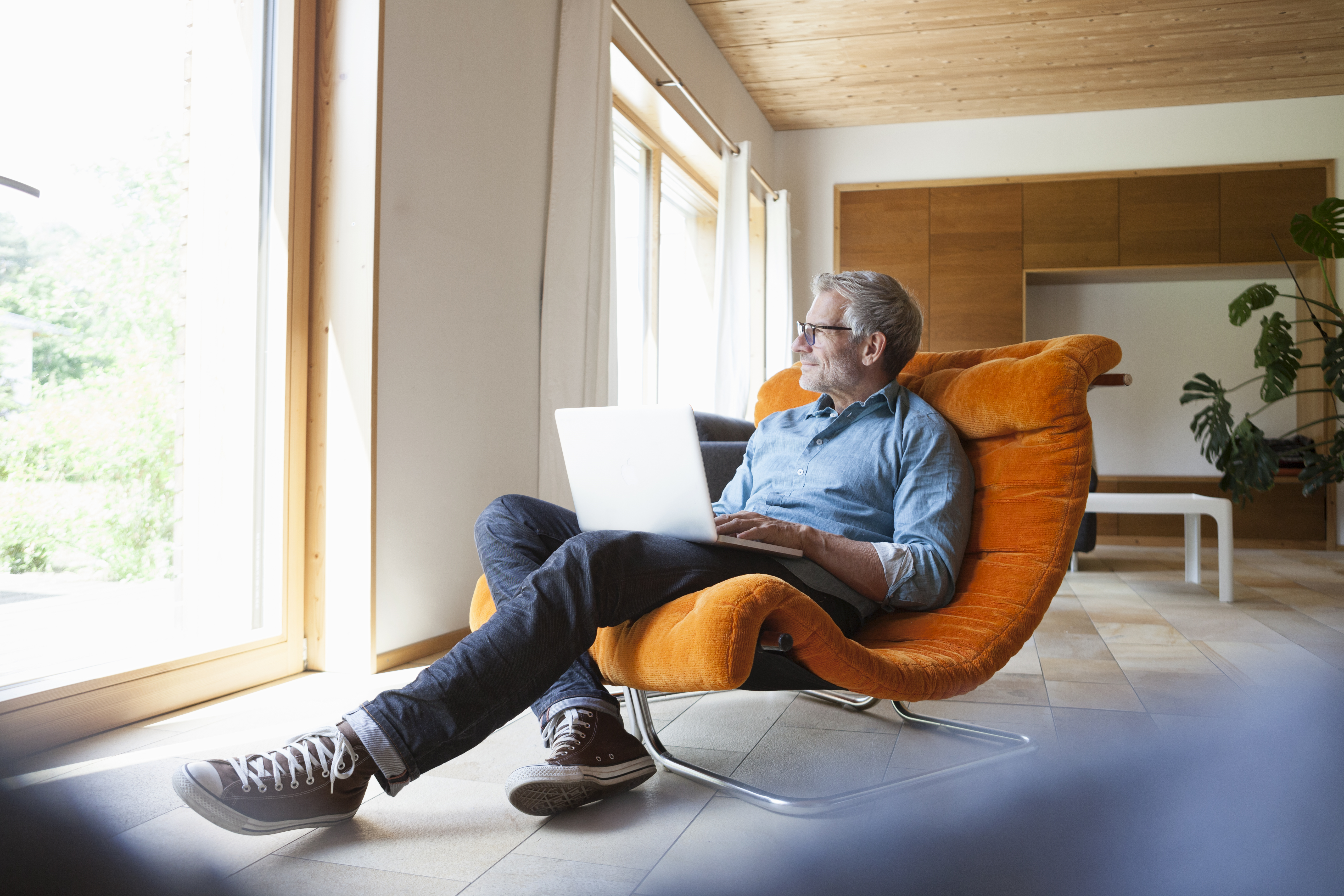
For facilities managers, technology can enable you to automate tasks and drive efficiency to save time and money. There are multiple facilities management (FM) software solutions, but only one, CMMS, focuses on managing work orders, vendors, and assets. When you leverage a CMMS powered by analytics and insights you can make faster, data-driven decisions for better FM performance.
The CMMS Solution to Facilities Management
The facilities management (FM) job role continues to expand as buildings become more complex and technologically advanced. In recent years, innovative technologies have introduced automation, analytics, and insights that streamlined FM practices and produce new and welcome effiencies for busy FM teams.
Today’s facilities managers (FMs) create budgets, analyze capital expenditures, control maintenance costs, boost energy efficiency, and pursue sustainability. They also manage techs and vendors and navigate ever-increasing expectations to achieve time- and cost-savings.
The scope of the facilities management role is daunting. Fortunately, FMs can leverage software, like a computerized maintenance management system (CMMS) to manage their fast-growing responsibilities while accelerating performance for better, faster decision-making.
These solutions intelligently extend the useful life of equipment, thereby delaying replacement, lowering capital budgets, and increasing ROI. The right software can identify optimal preventive maintenance schedules and then track repairs and upgrades to reduce the time spent fixing offline equipment.
“The volume of machines and equipment present in many buildings today requires a systematic management approach,” said Paul Liesman, vice president of engineering with Horizon Engineering Associates, a building commissioning and consulting firm.
“Gone are the days where you could just keep a list,” Liesman said.
In addition to administrative efficiency, many FM software solutions allow FMs to assemble large volumes of data and convert them into information that can improve decision-making, according to John Edwards, CFM and vice president, Facility Engineering Associates.
“Just as technicians have tools, like hammers and meters, a software system is a tool that enables facilities managers to more effectively do their jobs,” said Edwards.
A Trade Press White Paper Commissioned by JLL Technologies
But what type of software? The range of solutions available to help FMs covers everything from homegrown spreadsheets to an “alphabet soup” of software tools.
How a CMMS can help
A computerized maintenance management system (CMMS) helps FMs boost performance of corporate resources and assets, which drives greater value and reduces long-term costs.
John Rimer, CFM and president of facilities consultancy FM360, believes a CMMS is “the central nervous system” of the facilities organization.
“If you are not effectively using a robust CMMS, your facilities management program will not be successful,” Rimer said
A CMMS boosts FM effectiveness in several ways. Capturing the full and proper lifespan of the equipment in a facility requires ongoing, consistent maintenance. A CMMS can help document and determine the preventive maintenance schedule required. At the same time, a CMMS can document any unscheduled maintenance that occurs.
“Without this, you don’t know which pieces of equipment are failing or are more troublesome than others,” Liesman said.
When it’s time to create a capital budget, FMs who lack a record of the pieces of equipment that are causing problems are losing key data about how to develop and allocate their budgets.
The information contained in a CMMS also can help FMs advocate for the funding their departments require. Because a CMMS contains information on the equipment’s performance, repair history, and age, among other information, executives who manage budgets can easily identify where resources are needed and why.
That said, any number of alternatives to CMMS solutions can be found. In evaluating them, Rimer advises considering the lineage of any solution.
Most CMMSes emerged from the facilities and maintenance functions. They were developed to manage assets, work orders, and vendors, among other functions. Because they’ve been asset- and maintenance-driven, these functions are the strong suit of a CMMS. While alternative solutions may offer expanded functionality, they typically fall short of meeting the core requirements of a CMMS. Additionally, a broader solution can become cost-prohibitive and unwieldy for many organizations.
Spreadsheets and other homegrown solutions
Spreadsheets often are a starting point when a facilities department shifts from pen and paper to software. Edwards said they suffice in some cases. For example, an FM who oversees a
small, single building may find a whiteboard or spreadsheet is all that is needed to adequately manage the facility. Similarly, a facilities pro could use a calendar program to schedule, for instance, the dates for changing the filters on an air handler, according to Liesman. However, this is a rudimentary approach and will not enable comprehensive maintenance.
While spreadsheets and online calendars are clear steps forward from entirely manual processes, Liesman noted they lack some critical capabilities, such as automation. As a result, these tools tend to lead to cumbersome processes. For instance, a work order typically will list the preventive maintenance procedures required and the parts needed to complete the maintenance procedure. Some online systems may link to a digital version of the operations manual: “You click on a link, and all the information is there,” Liesman said.
But few spreadsheets or online calendars will have this depth of information. In addition, as FMs work with more, larger, and often complicated properties, they generally need to collect and share information in a consistent, accurate manner. A spreadsheet doesn’t really lend itself to this. Even when the information is on a shared drive or distributed via e-mail, it can become vulnerable to data-entry errors and inconsistent updating.
“It’s really the size and the scale of the operations that determine when you bump up against the limits of a spreadsheet,” Edwards added.
FMs who rely on spreadsheets often find themselves mired in reactionary mode, digging themselves into a deeper deferred-maintenance hole, Rimer noted. The administrative burden of updating and synchronizing data in spreadsheets further compounds this.
Moreover, even the most sophisticated and effective homegrown systems require ongoing investments of time and money to ensure continued accuracy and relevance. FMs need to account for this commitment of resources when assessing the cost-effectiveness of an internally developed system.
Per Edwards: Ultimately, FMs need to assess whether the system is providing information the organization needs to make sound, intelligent decisions. If not, it’s time to look for a solution that can.
Computer-aided facility management (CAFM)
Most CAFM systems trace their lineage back to the architectural world. As a result, these systems are great for space planning, project management, and occupant moves, according to Rimer. For instance, the solutions may offer interactive floor plans and be able to identify the work orders or different assets associated with a specific area. For hybrid workspaces, CAFM software can accept conference room and desk reservations and even pinpoint employee locations.
What’s the downside of CAFMs? They often surpass the functional requirements of a CMMS. As a result, they tend to be more expensive to implement and may require more updates and maintenance than the FM staff can practically manage.
“They can be too onerous and expensive for the facility department’s needs,” Liesman said.
Organizations that use CAFM programs often need to involve multiple areas in developing or managing the software, such as the facilities office, building management personnel, and perhaps the leasing staff. “CAFM is more of an integrated application,” said Liesman.
CAFM solutions also fall short when it comes to core maintenance management functions. Even if they incorporate these features, they’re often clunky or lack power.
“They’re strong on the floor plans and space planning but weak on the maintenance management side,” Rimer added.
Integrated workplace management system (IWMS)
The IWMS came out of the commercial real estate industry. For Edwards, the word “integrated” in IWMS is key. These solutions incorporate functions that help in the management of six key areas: real estate and lease management, space management, FM, sustainability, capital project management, and employee experience. Many IWMSes allow these departments to talk to one another or share information. As a result, organizations with large facilities portfolios trying to manage all those functions collectively, while also controlling the funding for them, would typically consider an IWMS.
What’s the downside? These capabilities often extend well beyond what the facilities department requires. Moreover, the solutions often are weaker on capital replacement planning, maintenance management, and other functions key to FM, according to Rimer.
Enterprise asset management (EAM)
EAM solutions also tend to be far more comprehensive, noted Rimer. In addition to tracking assets and maintenance, they may monitor inventory and manage invoicing and purchase orders, among other functions. Some include human resources capabilities, so as technicians complete work orders, they may be able to use the EAM to punch in and out on their timecards.
“They’ve really tried to capture both tangible assets and anything related to them,” Rimer said.
EAM solutions tend to be more organizational tools than facilities tools, per Edwards. Organizations might, for example, use EAMs to manage production-line equipment. They’re also often tightly integrated with a business’ financial management software.
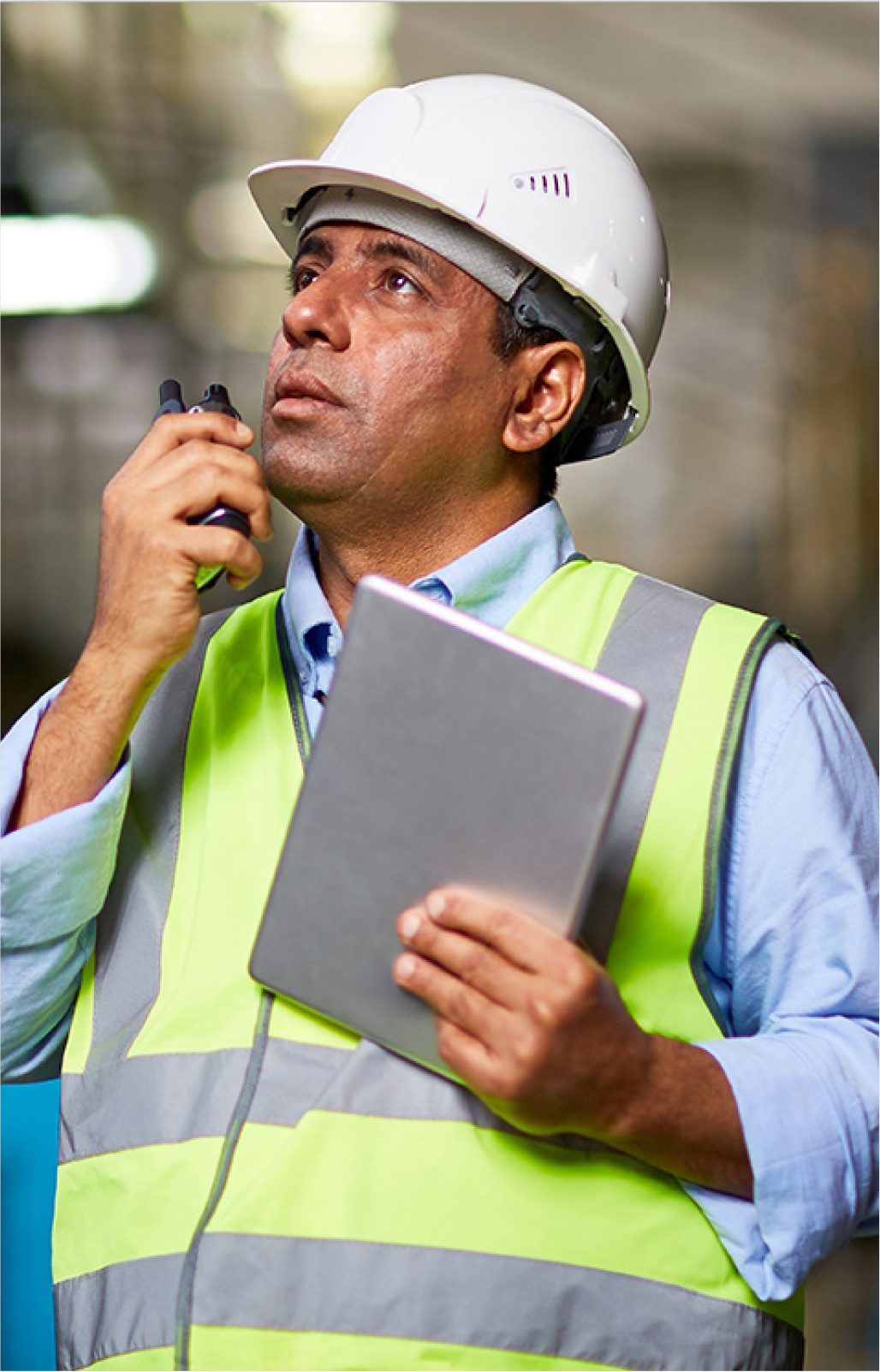
While such a comprehensive system can be immensely helpful, it can also be expensive. Rimer estimated he could purchase CMMS software licenses, complete data-gathering, and configure and implement the solution at a small- to medium-sized university for about $100,000. The cost for an EAM solution at a similar campus?
“You’re talking potentially millions of dollars,” said Rimer.
In addition, because the larger EAM systems are not solely focused on buildings, the functionality of their building modules is not always the strongest.
“Some systems don’t necessarily have great visuals or graphical space functions,” Edwards said.
The work order function tends to be like a help-desk function. So, FMs may be able to collect and assign work orders but then find it difficult to track details and generate the reports needed for building maintenance, as one typically could with a CMMS.
Why a CMMS is the best fit
Edwards explains that when it comes to the facilities functions: “A CMMS is the right tool for managing the operations and maintenance work of a facility or a portfolio of facilities. The information that can help an operations and maintenance department run better is really the focus of the CMMS.”
Moreover, CMMSes range from remarkably simple to extraordinarily complex systems that can help manage worldwide maintenance programs, according to Edwards. No matter the solution a facility needs, a CMMS likely will fit it.
Rimer noted that a CMMS is a “one-stop shop” for facilities departments. Most incorporate a database that can capture everything occurring within the facilities organization so everybody is operating with the same information. This streamlines communication and information-sharing and reduces manual transactions and, thus, errors.
JLLT’s CMMS, Corrigo, offers real-time syncing between mobile and desktop versions, ensuring that both update simultaneously, a valuable feature for techs and service providers in the field.
A CMMS can help identify and manage contract service providers. Today, many FMs rely on their personal networks to find, for instance, an expert who will work on the weekend to fix an HVAC system, according to David Rainton, head of FMPM products, JLL Technologies. While these networks and knowledge are important, they’re often inefficient and difficult to scale.
“Facilities managers need a technology solution that can identify the best-performing vendors,” explained Rainton. A powerful CMMS should also show which vendors underperform.
Another less obvious benefit of a CMMS is the way in which these solutions, because of the information they contain, help FMs more persuasively advocate for the funding they need.
“Most facility departments are underfunded because they haven’t been able to substantiate the level of resources they need,” said Rimer. “As a result, many are continually playing catch-up.”
FMs who can gather relevant information regarding their department’s operations and performance within a CMMS can then use it to promote informed business and budgeting decisions.
For many organizations, facilities are the second-largest expense after staffing costs, according to Rimer. When organizational budgets need trimming, management typically knocks on the facility department’s door, in lieu of staff layoffs and hiring freezes. The cause of this cost-cutting approach is partly due to management’s lack of understanding of the resources needed to sufficiently maintain the portfolio, as well as FMs’ inability to adequately convey such information.
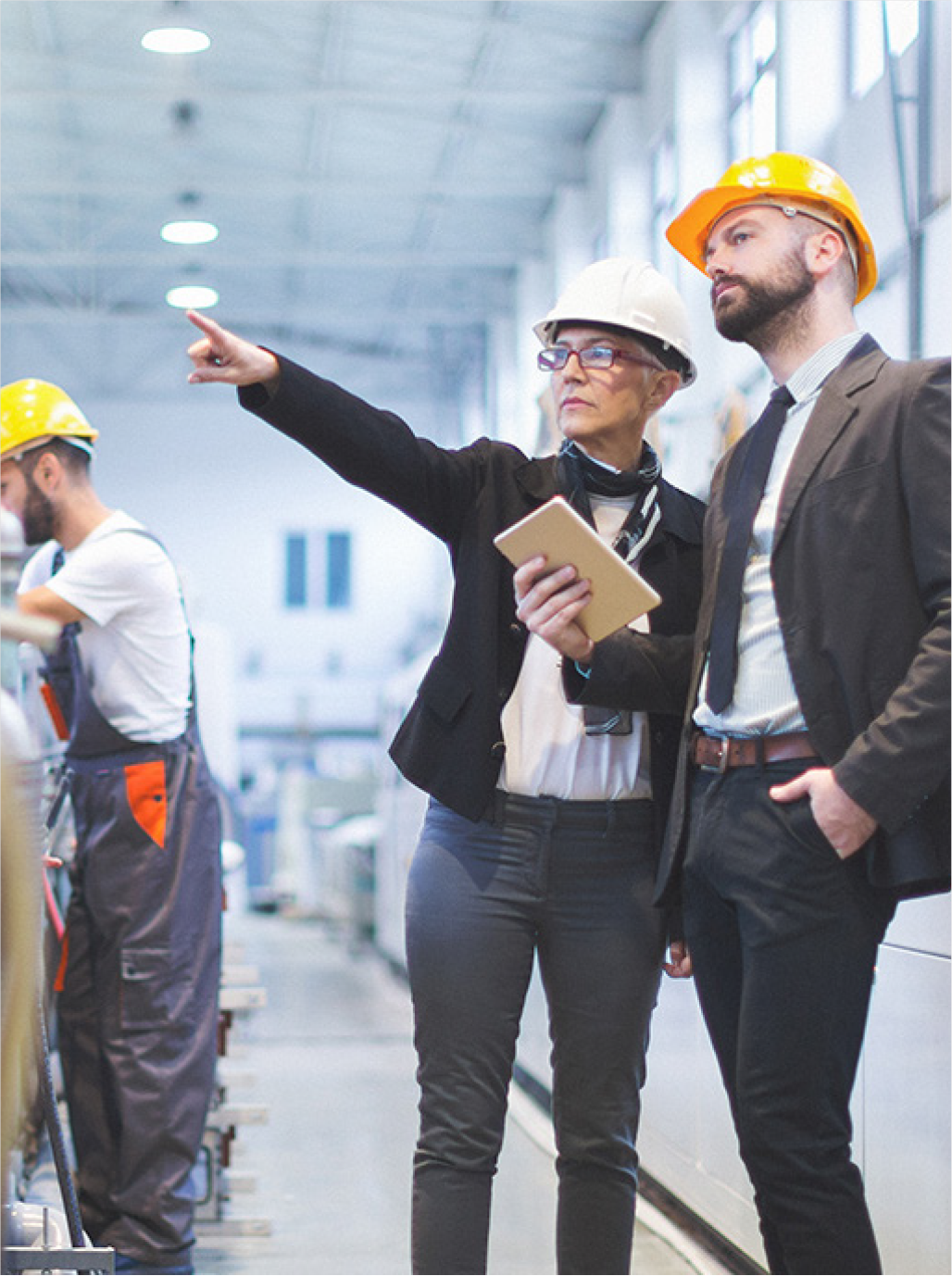
By tracking a comprehensive data set within a CMMS, FMs can both more effectively manage day-to-day operations and leverage the information to advocate for their efforts and the value their team provides to the organization.
“A CMMS really allows the facility manager to be more proactive. They can organize, plan, and implement and then track their work,” Edwards said. “It is a tool for doing things well.”
For instance, Corrigo, which is installed in 526,000 locations around the globe, can handle the numerous functions required for professional facilities management including:
- Managing work orders, assets, and vendors
- Establishing preventive maintenance workflows
- Documenting completed work
- Tracking equipment histories
- Benchmarking service providers and other capabilities
In addition, Corrigo’s mobile capabilities enable FMs to easily find, identify, and service assets on the go. The app allows real-time visibility into work order status for better and faster decision-making. The customizable interface offers convenience and ensures greater speed and productivity.
()A recent study conducted by Forrester Consulting on behalf of JLL surveyed decision-makers from organizations that had implemented Corrigo and revealed that the software reduced the time employees spent completing routine maintenance checks by 33% and drove greater data-driven insights. Total savings from these features topped $1.6 million over three years. In addition, streamlining invoice processing saved an additional $1.2 million over that same period. In total, the return on investment was 238%.
A recent study conducted by Forrester Consulting on behalf of JLL surveyed decision-makers from organizations that had implemented Corrigo and revealed that the software reduced the time employees spent completing routine maintenance checks by 33% and drove greater data-driven insights. Total savings from these features topped $1.6 million over three years. In addition, streamlining invoice processing saved an additional $1.2 million over that same period. In total, the return on investment was 238%.What to look for in a CMMS
As facilities become smarter, their ultimate custodian—IT or facilities—becomes more of a question.
“It’s so important for facilities professionals to be technology-conversant,” Rainton said.
That’s especially true when it comes to selecting a CMMS. The right CMMS, intelligently implemented, boosts efficiency and effectiveness within the FM department. To increase the likelihood a CMMS will meet your needs and be used, consider the following steps:
- Evaluate user-friendliness. When systems are inordinately complex or require a great deal of time to request or enter information, users often work around them. To avoid that, look for systems that perform the functions you need—but don’t include more capabilities than you’ll use: “Be very realistic,” Liesman said.
- Also involve the team that will use the system in selection process. For example, if technicians in the field can upload information remotely, the system will save time and cut errors, encouraging its use. Ensure they can enter work orders relatively easily and intuitively.
- Identify any compatibility issues with the systems you already have: “How well does the software play with others?” Rimer asked.
- For instance, application program interfaces, or APIs, allow the CMMS to share information with other systems, such as accounting systems, with relative ease.
- Review the mobile interface. Rimer noted that the goal is to make sure the actions required to use the interface are simple and intuitive. This will promote adoption by field engineers that may be wary of using mobile devices or leery of the small but additional effort needed to capture this invaluable information.
- Assess the solution’s flexibility. Many systems will initially suffice to meet the needs of the FM team. However, once they ask the system to do something a bit outside its rigid box, the
- manager quickly grows frustrated with its limitations, according to Rimer. For example, imagine you complete a work order and want the system to generate a resulting action, such as an update to the equipment status to show it’s no longer offline. The right CMMS should allow you to handle this within the system itself—without having to pay for customization.
- “Ideally, the software provides enough tools to stretch the edges of the box, maximizing the value of the system to the organization,” said Rimer.
- Evaluate the reporting functionality. How well and easily can you get information from the system? Does it allow you to customize reports or enter queries that can help answer questions? In the end, one of the main reasons for having a CMMS is its ability to enhance decision-making—and that requires robust reporting capabilities.
- Assess the training materials provided. Few FMs have the resources to train themselves on a new system, let alone their employees or outside service providers, Rainton noted. Recognizing this, Corrigo provides a wealth of training materials, including videos and webinars.
Nine keys to successful implementation
As with any software or tool, a CMMS that’s not thoughtfully chosen and implemented can become an obstacle people have to work around. Here are the keys to a successful CMMS implementation:
- Rimer shared that it’s key to figure out what you need before choosing the system. For instance, decide if a training module is necessary. Determine if the system will need to manage utilities. Distinguish what he calls “need-to-have versus a nice-to-have.”
- Fix any broken or weak processes before installing a new system: “If you apply a CMMS on top of a broken process, you’re just going to have a really digitized, fast, broken process,” Edwards said.
- Similarly, check data cleanliness and accuracy: “If you don’t have good data going in, you’re not going to have good data coming out,” said Rimer. This includes information on the facilities and assets themselves, as well as preventive maintenance. If this data is in good shape when you launch the CMMS, you can hit the ground running.
- Consider the conversion cost, cautioned Edwards. If you’re replacing an existing CMMS, how easy is it going to be to get information from one system to the other?
- Be open to change. When upgrading or replacing any system, including a CMMS, there’s a tendency to want to avoid upending entire processes and functions. That can undermine the benefit of implementing a new system in the first place.
- “You might have to question some old processes, especially if they limit efficiencies in the new CMMS” said Liesman.
- Rely on your commissioning agent to identify equipment. In new construction or major renovations, many changes likely have occurred from the original equipment schedule, often due to costs or schedule constraints, noted Liesman. The agent will have the latest list of equipment.
- Ask vendors to show how their systems can complete the steps you know your solution will need to perform. They should be eager to provide an actual, live demonstration of the software handling these functions.
- “Tell them not to just show screenshots or a presentation that says our software can do it all,” explained Edwards.
- Get buy-in. Per Liesman: To minimize the risk that a system will end up on a shelf collecting dust, obtain buy-in from those who will be using and maintaining it.
- Identify who will maintain and administer the CMMS. You need an individual or outside entity dedicated to this function, according to Rimer.
Next steps:
Corrigo is the leading CMMS for the facilities management industry. It’s automates and accelerates work orders, vendor management, and asset maintenance. It helps busy FMs and their teams become more productive by eliminating time-consuming, manual tasks. The FM job role becomes far less daunting when technology streamlines traditional processes and frees the FM team for higher priority work.
To learn more about our CMMS, ()contact a Corrigo expert today.
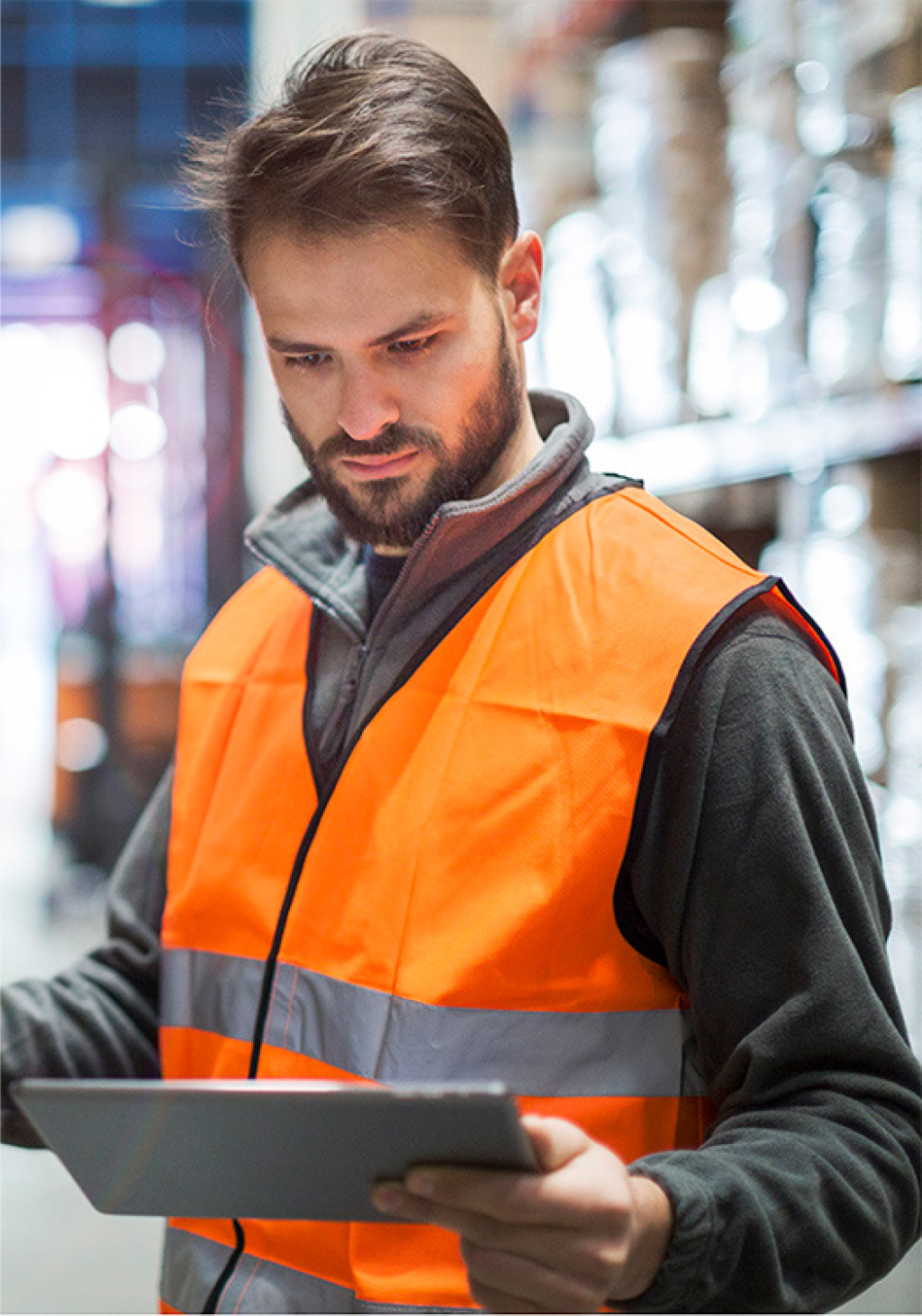
JLL Technologies
Four Embarcadero Center, Suite 1500
San Francisco, CA 94111
USA
Tel: +1 (415) 612-3233
A white paper commissioned by JLL Technologies. © JLLT 2022.
All rights reserved. Printed in the USA. Part #153-SBT-069