Retrocommissioning: New Low-hanging Fruit for Energy Savings
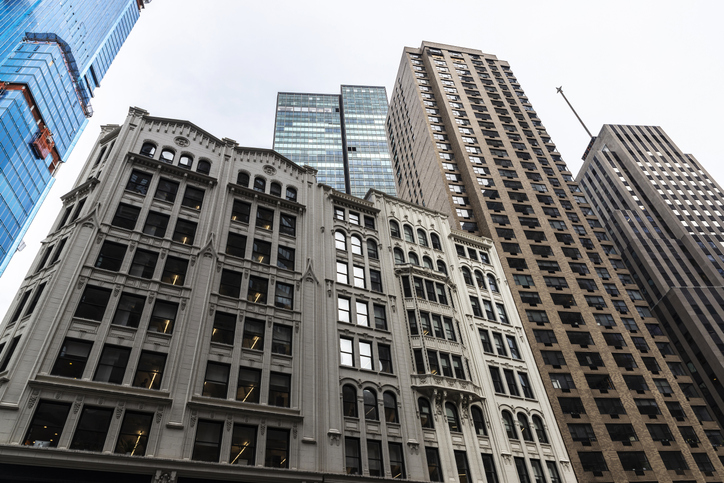
An introduction to retrocommissioning opportunities, process and benefits, including case study findings and common themes of retrocommission projects.
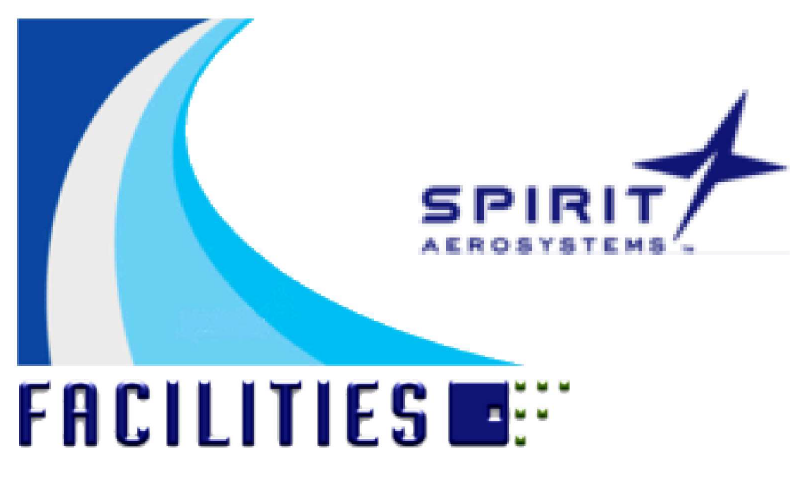
RETROCOMMISSIONING (RCx) New Low Hanging Fruit for Energy Savings
Certain content used in this presentation expressly authorized for use by RetroCom Energy Strategies, Inc.© 2008 Presented 5/1/08 at IFMA Industry Forum Spring Council Meeting

An Introduction
- Commissioning (Cx) performed during original project design and construction.
- RetroCommissioning (RCx) performed for existing buildings that were never commissioned or not commissioned properly
- Walker's Definition -A systematic, organized, structured, and documented process to examine all building systems, envelope, and structure to ensure that all building components and systems are meeting current customer needs, functions, and interactions as designed and intended.
- Recommissioning -periodic testing, adjusting, and/or repair to maintain performance achieved during original Cx or RCx process
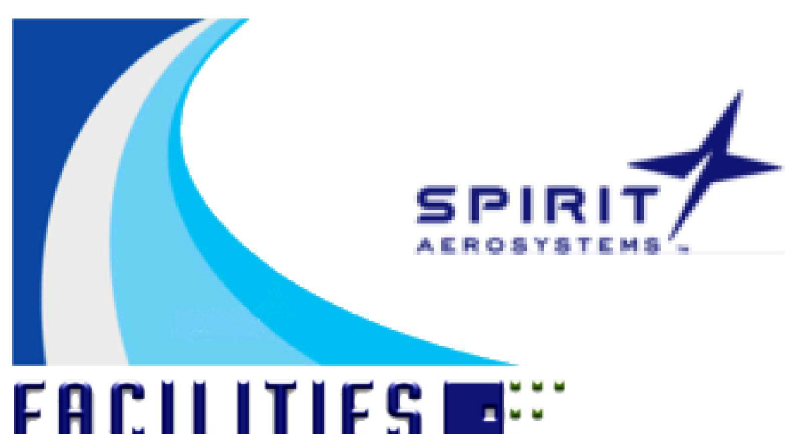
F R C I LI T I E S ■::.
RETROCOMMISSIONING (RCx) New Low Hanging Fruit for Energy Savings
- Texas A&M Energy Systems Laboratory studies over the past15 -20 years -Continuous Commissioning™
- -Documented $millions in energy savings
- ASHRAE Guideline 0-2005
- Independent studies by Universities, DOE and others • Several evaluations by the California Energy Commission, NYEC, other states since 2000
- Included in USGBC LEED EB® rating system
- Adopted by the State of California as standard for all state buildings 50,000SF and over -every 5 years
- Utility Rebates in California and other states starting -2006 • Quickly gaining popularity for reasons we will reveal today

D

Why Retrocommissioning Opportunities Exist
An Unfortunate Definition Of Retrocommissioning
- -Commissioning a building after it has been constructed and occupied
- -Finding and repairing deficiencies that are left over from the design and construction phase
- -Discovering preventive maintenance problems and opportunities
- -Providing Building Maintenance & Operations training that was "value engineered" out at the construction phase -Rewriting the Service Maintenance specifications to ensure
- that tasks produce performance & real outcomes
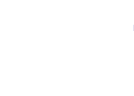

Case Study Findings
- Opportunities are similar building to building
- Design flaws & Construction defects
- Equipment & Systems malfunctioning
- Symptom Driven Demand/Repair Maintenance
- Inappropriate Preventive Maintenance
- Lack of systems understanding
- Little commitment to provide ongoing training


What are the outcomes?
- A variety of performance deficiencies
- -Occupant Comfort complaints
- -Premature equipment failure
- -IAQ challenges or..................... Liability?
- -Absolutely unnecessary energy use & cost
- Significant confusion regarding the root cause
- -It's the control system or vendor
- -It's the maintenance contractor
- -It's the equipment or device
- -It's the building operator
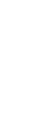

The Common Themes
• Construction Defects
- Generally from the absence of Commissioning
- Nobody is looking out for the owner's interest
- Low Bid = skinny margins = corners cut
• Design Mistakes
- Boiler Plate specs create a high rate of misapplication
- -Risk mitigation by over sizing -up to 15% is common
- Project cost pressure & urgency
- a I ue E ngIneenng• • -• .......a misnomer. '
• Maintenance Issues
- Poor commitment to training ....... not poor maintenance
- Minimal in house support ...... not a lack of maintenance
- Most often ............... THE WRONG MAINTENANCE
Our Construction Mentality
• Buildings cost more to operate than to build
- -Value Engineer all the training out at the contract stage
- -Expect Building Operators to have professional engineering skills
- -Apply maintenance paradigms that produce the wrong outcomes
- -Blame the service contractors for all the equipment problems
- -Cut the maintenance budget year after year
What are some of the indicators?
- Excessive weekend/night energy use
- Excessive equipment noise
- Excessive HVAC system pressure drops
- Displayed temperatures that make no sense
- Broken, disabled or overridden controls
- Occupant complaints -hot, cold, stuffy, etc
- Energy bills that keep rising
How big is the opportunity?
- According to Energy Star® the conservative opportunity for Retrocommissioning based energy cost reduction in the United States is $18 Billion ! !
What can we impact?
- We can't stop the construction defects
- -The building is already built
- We can't stop the design challenges
- -The design is complete and in place
- WE ABSOLUTELY CAN SOLVE THE OPERATIONS AND MAINTENANCE ISSUE!
- -In fact in existing buildings that is all we can do and it is the most important thing we can do!
- -And doing so will solve 90o/o of the problems we encounter!
- -And it will pay for itself!
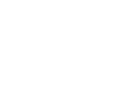
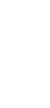
Out of Sight, Out of Mind!
Flexible ductwork conditions like these are common -Creases and folds decrease flow and volume, add to demand at the fan, and increase potential for ductwork rupture
Installation Issue
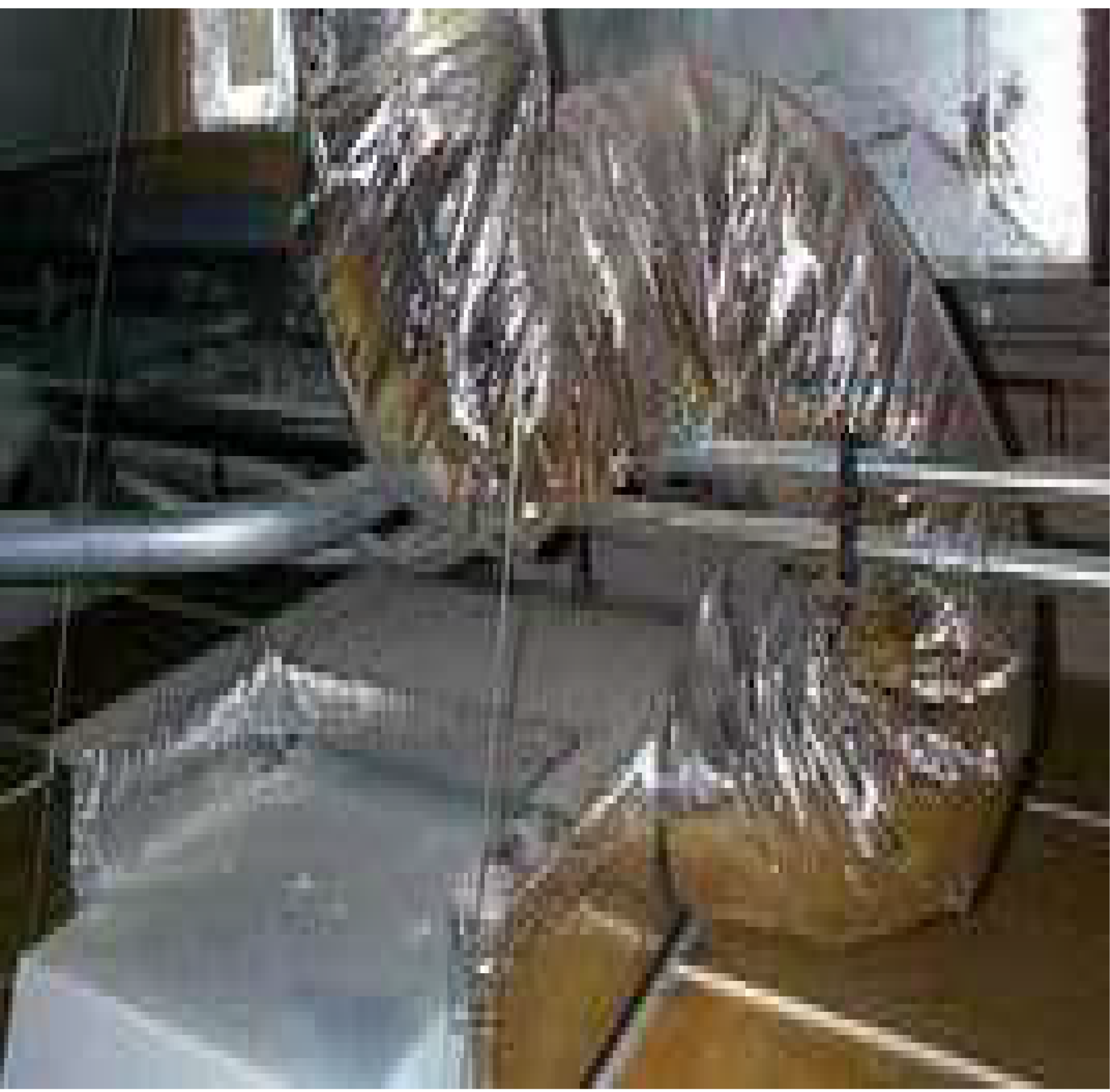
RetroCom Energy Strategies, Inc. © 2008
Outdoor Air Sensor placement can be critical.......
How do you think this one will work?
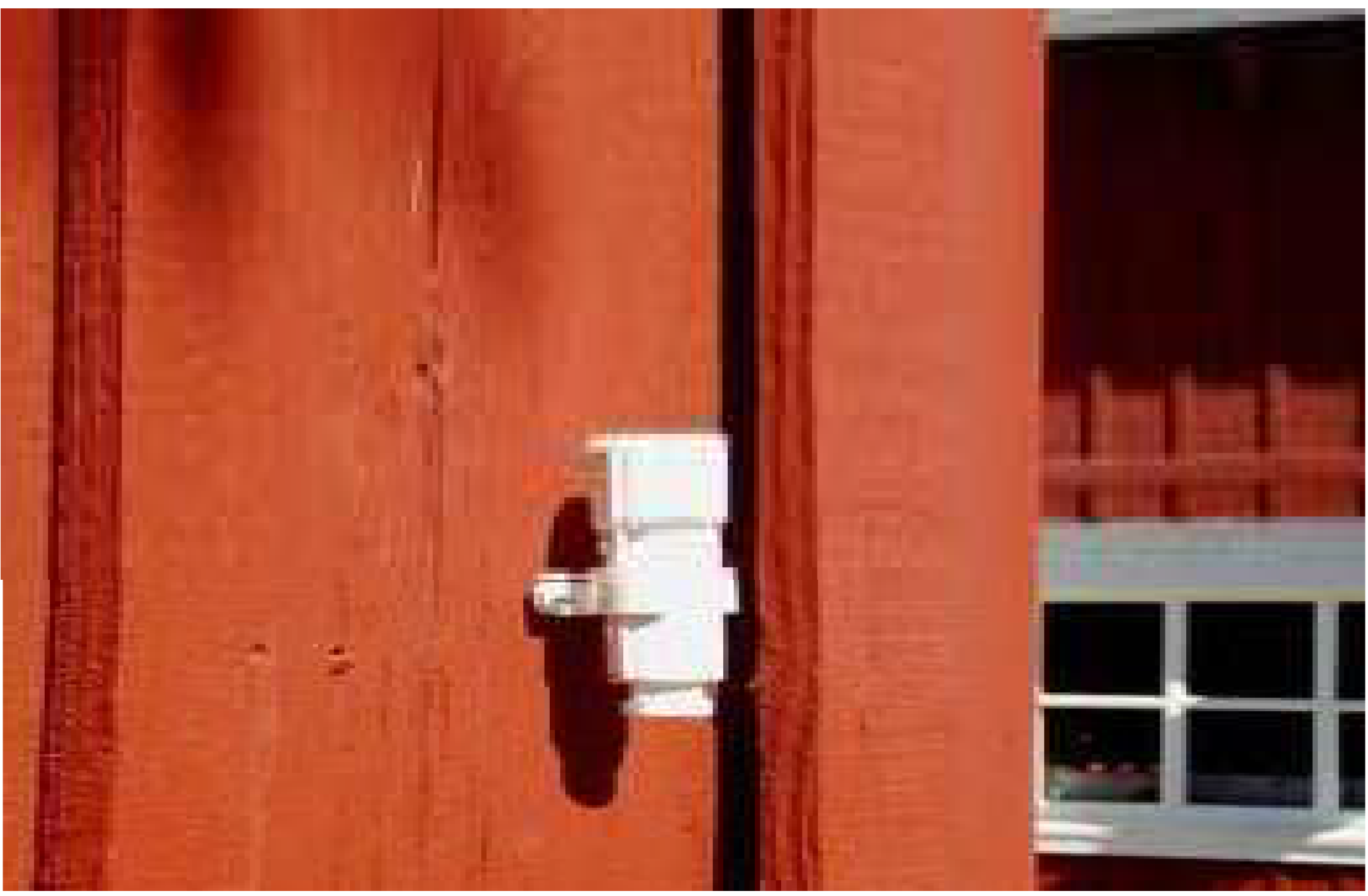
RetroCom Energy Strategies, Inc. © 2008
Installation or Design?
Static Pressure Sensor is too close to the supply fan to deliver appropriate control at the zone level This building had a history of ventilation complaints

RetroCom Energy Strategies, Inc. © 2008

A favorite........ Maintenance failed to discover that the damper linkage was actually disconnected The actuator motor worked fine but the dampers never moved!
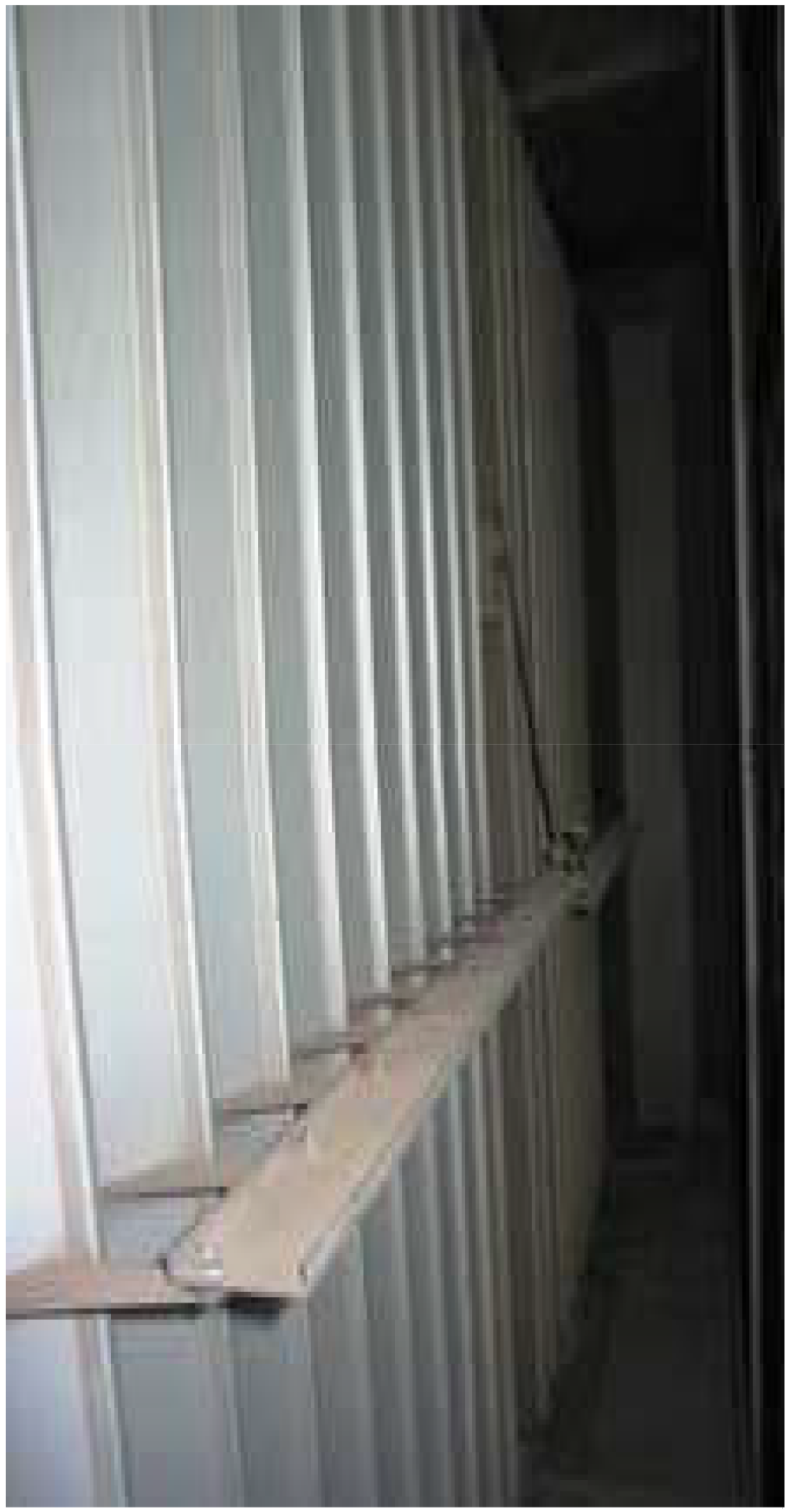
A false sense of security?
Many of the VFD's installed at this site were found to have status readings that had no relation to actual fan or motor function -some were bypassed altogether
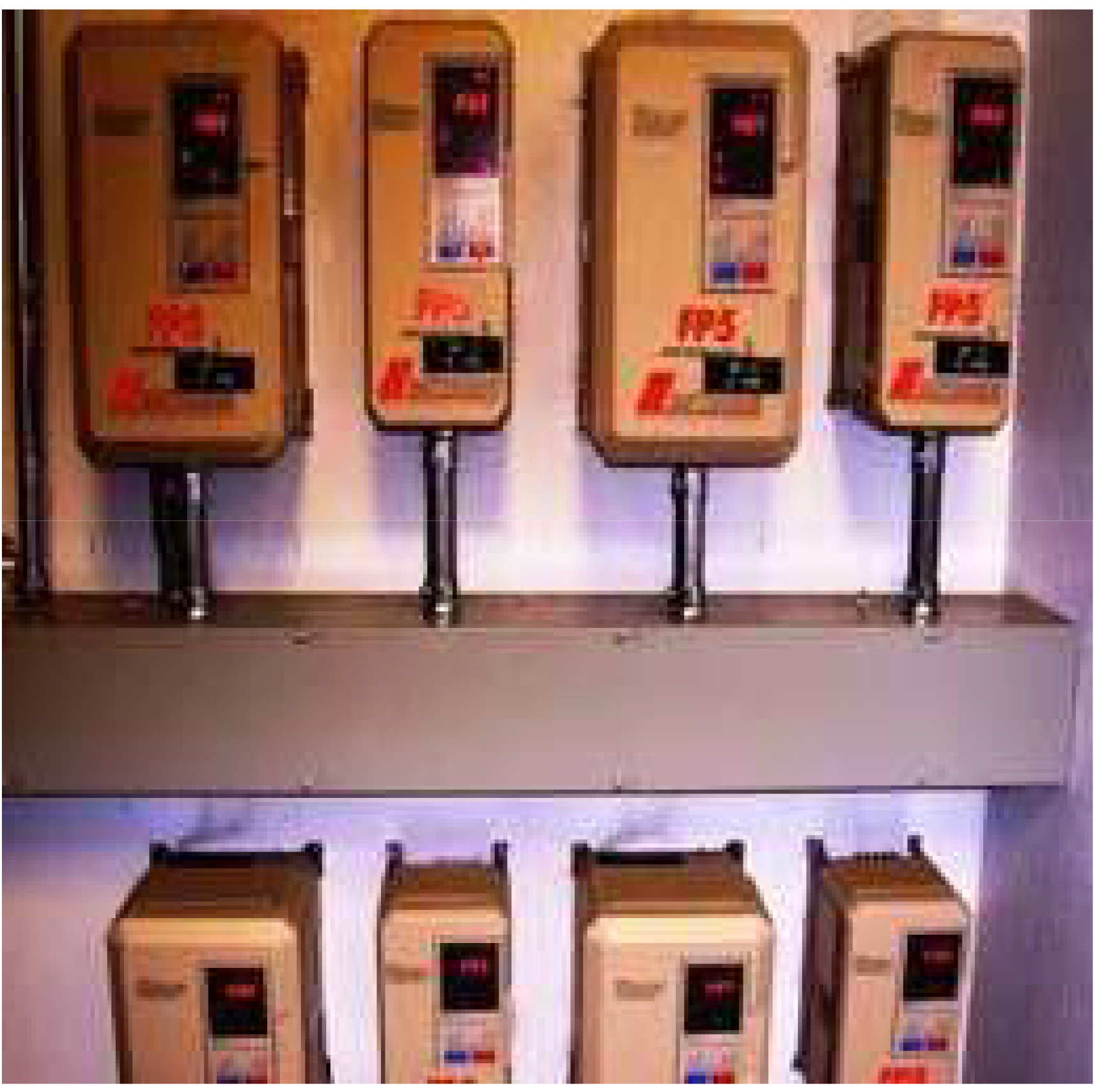
RetroCom Energy Strategies, Inc. © 2008
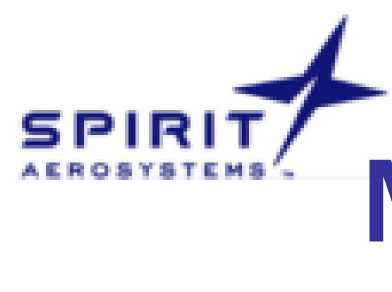

.!ff-Maintenance Does Impact Energy
- Include maintenance tasks that provide relevant information about equipment condition and operation
- Is damper linkage connected?
- Do damper actuators actually operate?
- What condition are the damper blades in?
- Are minimum positions being maintained?
- Are VFD's actually working?
- Are Inlet vanes operable?
- Is simultaneous heating and cooling taking place?
- Is sequential heating and cooling taking place?
- Are Reset temperatures accurate?
- Are Valve positions equal to feedback?
- Is water traveling in the correct direction?
- Is device calibration accurate?
-Ł--=---.r.l.Ł.!Łhange the Maintenance Paradigm
- Evaluate current maintenance practices.
- Begin to understand that O&M procedures can have a significant impact on energy.
- Check and Inspect is close to worthless without tasks that produce outcomes.
- Review and alter Maintenance Contracts to contain value -hold your provider responsible.
- Begin to focus on equipment performance.

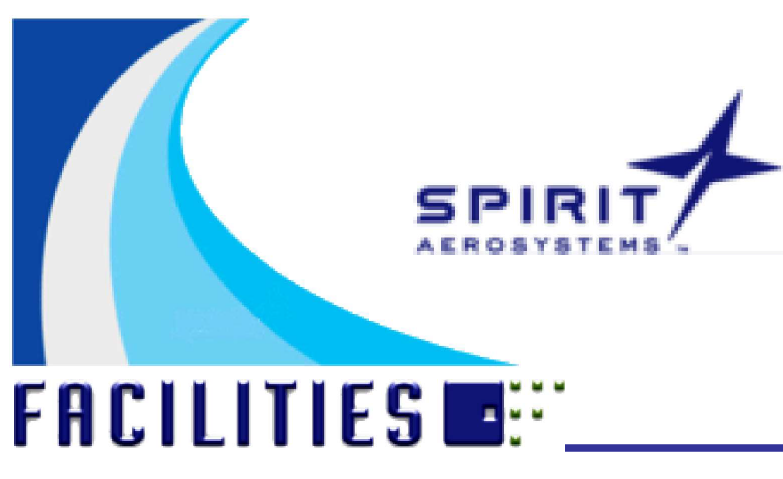
Changing the Paradigm
- Change maintenance procedures to include tasks that, discover deficiencies left over from design or construction
- Inspect and validate the operation of equipment.
- Witness it first hand -have your contractor prove equipment
- operational sequences.
- Write the procedures into your maintenance plan
- Focus on those tasks that actually ensure the equipment or system is performing efficiently.
- Focus training on issues that can actually add value and reduce operating costs.
- Build commissioning skills into the maintenance process to ensure that efficient equipment performance is sustained.
RCx Rewards -Non-energy
- Reductions in equipment failure & repair costs.
- Reductions in IAQ challenges and liability.
- Reductions in occupant complaints.
- Reductions in deferred maintenance.
- More time to do real work.
- Better value from contract dollars spent.
- More effective allocation of resources.
- Opportunities to enhance maintenance outcome.
- Better staff retention thru investments in training.
F R C I LI T I E S ■::.
Case Study
■ Marriott has utilized RCx as a part of their energy demand strategy across their whole portfolio even renaming it to MRCx.
- -Resulted in 11million/yr savings
- -LAX -Marriott identified $153,000 energy savings that were no or lost cost measures.
- -San Diego Marina Marriott identified $306,000 energy savings at an implementation cost of $221,000 for ROI of 0.7 years.
- -Energy Star Program -They have documented and benchmarked 100% of their properties through their MRCx program leading to 120+ properties receiving the Energy Star label.
- Energy Star recognizes a documented EB CxP program for points towards labeling.
- The LEED accreditation process for existing buildings closely follows the EB CxP process.
Summing Up
- RCx is an relatively low cost method of providing significant reductions in operating costs.
- Because most existing building were not Cx'd there is likely an opportunity in your own building.
- As the financials indicate -this really is "low hanging fruit."
Want even more Content?
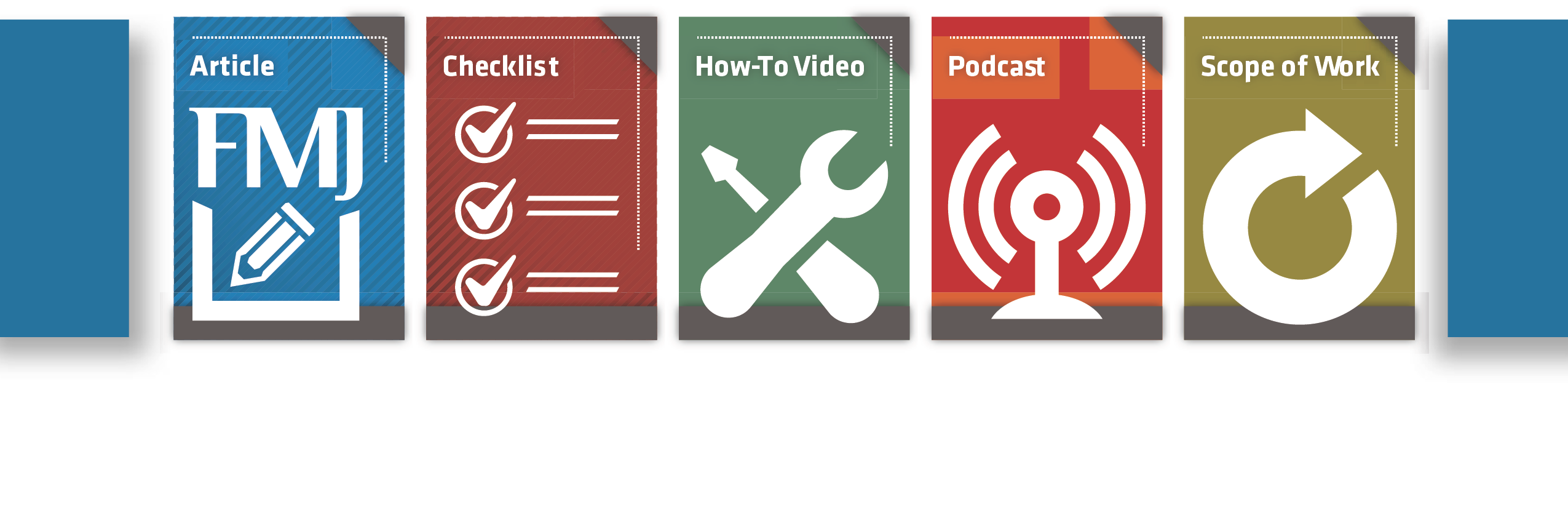
Since you’re already a user, you know that IFMA’s Knowledge Library offers all FM content in one place. But did you also know that by signing up via email to become a registered user, you can unlock even more resources?
Signing up via email for registered access within the Knowledge Library brings more content and functionality to your fingertips. Expect to grow your facility management knowledge, career and network faster than ever before.