Reduce Operational and Embodied Carbon in Commercial Buildings with Modern Building Controls
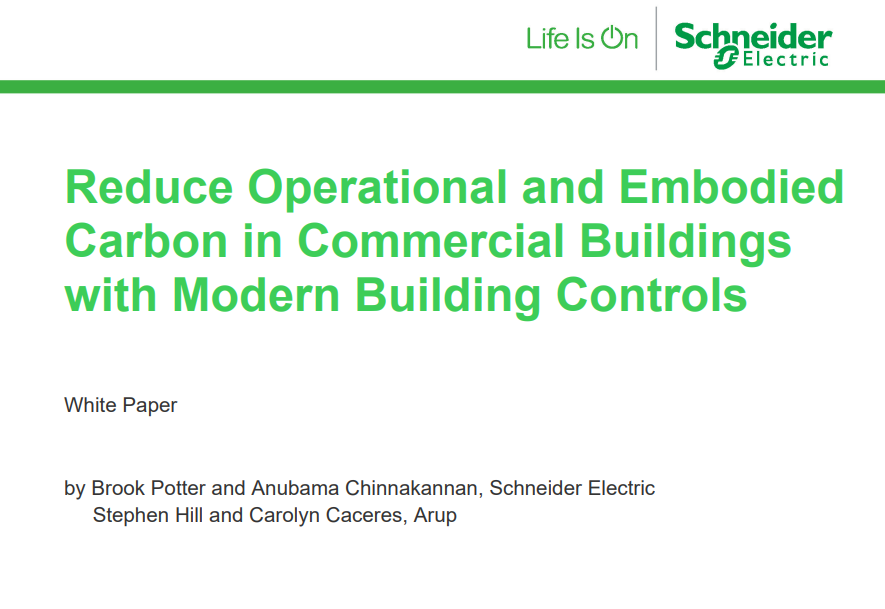
Arup, a global leader in sustainable engineering services, partnered with Schneider Electric on a technical research study to quantify how the performance of modern building controls in a Building Management System (BMS) could improve energy and car-bon reduction versus traditional building controls. Both controls solutions were based on Schneider Electric product offerings. This paper provides a synopsis of the broader study and findings showing, that in the scenario explored, modern BMS controls with room-level capabilities offered up to 39 percent of HVAC and lighting energy savings, which equates to approximately 26 percent reduction in whole building Energy Use Intensity (EUI). as well as 23 percent lower embodied carbon than traditional BMS controls.
Reduce Operational and Embodied Carbon in Commercial Buildings with Modern Building Controls
White Paper
by Brook Potter and Anubama Chinnakannan, Schneider Electric Stephen Hill and Carolyn Caceres, Arup
Executive summary
-
-
-
-
Arup, a global leader in sustainable engineering services, partnered with Schneider Electric on a technical research study to quantify how the performance of modern building controls in a Building Management System (BMS) could improve energy and carbon reduction versus traditional building controls. Both controls solutions were based on Schneider Electric product offerings. This paper provides a synopsis of the broader study and findings showing, that in the scenario explored, modern BMS controls with room-level capabilities offered up to 39% of HVAC and lighting energy savings, which equates to approximately 26% reduction in whole building Energy Use Intensity (EUI). as well as 23% lower embodied carbon than traditional BMS controls.
Introduction
Commercial office buildings need to become more intelligent, resilient, and responsive so they can more easily adapt to the evolving business needs of owners and occupants. As industry requirements are driving owners to deliver better energy performance outcomes in their buildings, including lower carbon emissions, one of the ways owners can achieve this is through more efficient building operations with system components that have less embodied carbon. Energy performance and reduced carbon emissions are becoming more imperative, given top-down government regulations, rising energy prices, and the broader need to address the global climate emergency.
One of the ways building owners can deliver on these needs is with modern BMS controls that can help make commercial buildings:
- More responsive to the experience and needs of occupants.
- 'Future-proof' by reducing the need for control system hardware upgrades and simplifying building reconfigurations.
- Less carbon intensive by lowering embodied carbon and operational emissions in support of broader net-zero objectives.
Arup's technical study sought to qualitatively and quantitatively compare traditional BMS controls versus more modern BMS controls in a commercial office project. The study was conducted in two phases:
Phase 1 - Capital project performance that assessed capital cost and embodied carbon of systems.
Phase 2 - Operational performance that assessed energy efficiency and operational carbon.
This paper provides a summary of key elements of the study to help readers evaluate and understand the advantages of a modern, connected BMS. It begins with an explanation of the difference between traditional and modern BMS controls. Then, the study's scope and basic methodology is described. Finally, results and findings are shared comparing the two systems.
Definition of Traditional vs. Modern BMS controls
Building Management Systems are critical for operating a building safely, efficiently, and reliably. However, increasing operational focus on energy efficiency and sustainability combined with fundamental changes in owner and occupant needs are straining traditional controls implementations, requiring them to evolve. In parallel, industry advancements in IT, cloud computing, IoT, analytics, and artificial intelligence are leading to new and broader capabilities in building management. ‘Traditional controls’ in buildings typically represent a single system (such as HVAC) or multiple discrete systems that each have separate controls, cabling, and other components. This represents a duplication of materials which leads to higher embodied carbon and costs. Traditional controls in a BMS may be loosely coupled to other control systems including lighting, fire control, and access control, where data points are pulled from those systems and displayed in the BMS software for added context or situational awareness. Additionally, traditional BMS controls use a limited number and types of sensors such as, ambient temperature and occupancy, and depend heavily on knowledge of BACnet. And traditional BMS controls often rely on larger zone-level control at a floor or even a building level (versus more granular controls at the room-level) so they have limited ability to manage energy use or occupant comfort in a more granular way.
Figure 1
BMS implementations and depth of integration with other systems is evolving as pressure grows for systems to be more efficient, sustainable, and capable of meeting changing occupant needs, including the use of emerging technologies.
The items in yellow in the box to the right reflect capabilities that were elements of the systems in this study.
By comparison, more ‘modern’ and tightly integrated BMS control systems may share common cabling, controllers, and other components thus reducing materials and embodied carbon. Additionally, as tenant and occupant space requirements change over time, reconfiguration of modern BMS controls can be accomplished more easily using software, which helps reduce churn costs and avoid embodied carbon for ‘rewiring’ system components which may not need to be moved or changed. Importantly it also increases the likelihood that reconfigurations will be carried out properly, which in turn should improve both energy and comfort outcomes, although evidence for this is anecdotal.
Functionally, modern BMS controls are more aligned with evolving industry requirements (e.g., greater emphasis on energy efficiency, sustainability, occupant comfort) and increasing technical capabilities (IoT, cloud computing, analytics, AI, low-cost sensors). Deployments of modern controls are generally larger in scope with more sensors and enjoy tighter integration with other smart building systems, including delivery of room-level capabilities. (See Figure 1 highlighting the evolution of systems and what is possible, illustratively.)
Modern BMS controls take better advantage of newer IT protocols and can be software-defined, making these systems much easier to deploy, setup, and reconfigure as building uses evolve over time, thus making the system and building more ‘future proof’. For example, software-defined zoning improves the lead time for floor layout changes in the control system from weeks to minutes. Users can make the changes through a web browser versus having BACnet experts make programing changes at the physical devices. Another example is the inclusion of Web Services through RESTful APIs in the building controllers which makes it much easier to connect to and integrate with other building systems (e.g., room booking systems) to further enhance control and improve occupant experience. The modern BMS control system represented in the Arup study are Schneider Elec-tric’s BMS application, EcoStruxureTM Building Operation and EcoStruxureTM Connected Room Solutions.
Phase 1: Scope and Methodology for Capital Project Performance
Arup modelled one floor of a theoretical commercial office building in London (see Figure 2 below) to compare the performance of a modern BMS with room-level controls against a traditional BMS controls configuration. The project included a 945-square meter generic ground floor office plan with a 1.5-meter planning grid, and the architectural program and floorplan reflected post-pandemic considerations.
Figure 2
Image showing the one floor theoretical office building modelled by Arup for the study: post-pandemic, dynamic office plan with partitions and furniture
© Arup
This included a reception area with lift access, a café, and restrooms as fixed areas. Comparatively, the office space reflected an open plan with flexible work, learning, and presentation spaces as well as perimeter partitioned meeting rooms. Furniture and fittings were selected to support better connection with colleagues and provide a better in-office experience. The space is anticipated to change as the business needs of the occupying organization evolve, and such reconfigurations may happen every two to six years. Examples of changes could include the addition of more dedicated offices or small collaboration rooms if there is less emphasis on flexible workspaces in the future.
For the study, Arup planned a typical commercial office HVAC solution with a minimum fresh air system ducted at high level and fan-coil units providing local heating and cooling (See Figure 3). Financial costs and embodied carbon for the traditional and modern controls installations were calculated using Schneider Electric pricing and Product Environmental Profiles (PEPs) respectively. This provided an objective comparison of the long-term cost implications of each system and framed an understanding of the pros and cons of each as well as potential future product development needs.
Figure 3
Image showing the one floor theoretical office building modelled by Arup for the study: post-pandemic plan with lighting, FCU’s and diffusers. The lighting is in blue, the FCUs in red.
© Arup
For the traditional BMS controls configuration, Arup and Schneider Electric agreed that traditional power distribution, hardware, and controls would consist of a Digitally Accessible Lighting Interface (DALI) lighting control system and a separate BACnet control system for HVAC controls.
Comparatively, the modern BMS controls configuration would consist of room controllers with extension modules for DALI lighting and automatic blinds. This included a BACnet data communication protocol for building automation and control networks, which allowed real-time interrogation of energy and performance data and control of the building environment.
Traditional BMS Controls Configuration
Figure 4
Traditional BMS controls scenario:
- This ‘traditional’ floor-level configuration uses a BACnet protocol for HVAC controls.
•A separate DALI network protocol is used to support lighting control, including occupancy-based sensors.
•There is limited ability for occupants to have a room or zone-level controls experience, beyond selected meeting rooms.
•The lack of other sensor data limits the ability for the space to respond more dynamically to occupant needs.
The traditional BMS controls set up consisted of the BMS and an automation server, connected to a network automation controller (NAC), allowing the BACnet communication protocol for building automation and energy metering and a separate DALI network protocol for the control of lighting. The NAC was connected to three gateway controllers. This allowed the control, commissioning, and monitoring of the lumi-naire ballasts, and ceiling-mounted Passive InfraRed (PIR) sensors allowed presence-controlled lighting. The perimeter meeting rooms and offices included additional separate wall-mounted lighting and HVAC wall controllers with temperature sensors to allow meeting room visitors to override settings for the lighting and temperature within the room. Three additional temperature sensors were required for the reception, café, and open plan office space. Manually controlled window roller blinds were specified throughout. (See Figure 4.)
Modern BMS Controls Configuration
The modern BMS controls components included an automation server, daisy chain BACnet connected to a series programmable room or zone controllers. The sensor bus allows connection of the sensor and controller components. Additionally, DALI lighting or automatic blind extension modules were connected to the room controller. This enabled automatic blind control and 24V power supply for interior motorized roller blinds. Wall controllers were selected to allow occupant control in the meeting rooms and for blind control throughout. (See Figure 5.)
Another differentiating element of modern BMS controls is a Bluetooth-enabled insight sensor that can capture several data types including:
- Motion detection / occupancy
- Ambient lux level /daylight detection
- Temperature
- People counting
- Sound level
- Humidity
Figure 5
Modern BMS with room-level controls:
- This diagram depicts a modern BMS controls configuration that deliver zone and room-level capabilities for occupants.
- The room controller offers extension modules for the insight sensor as well as lights and automatic blinds control.
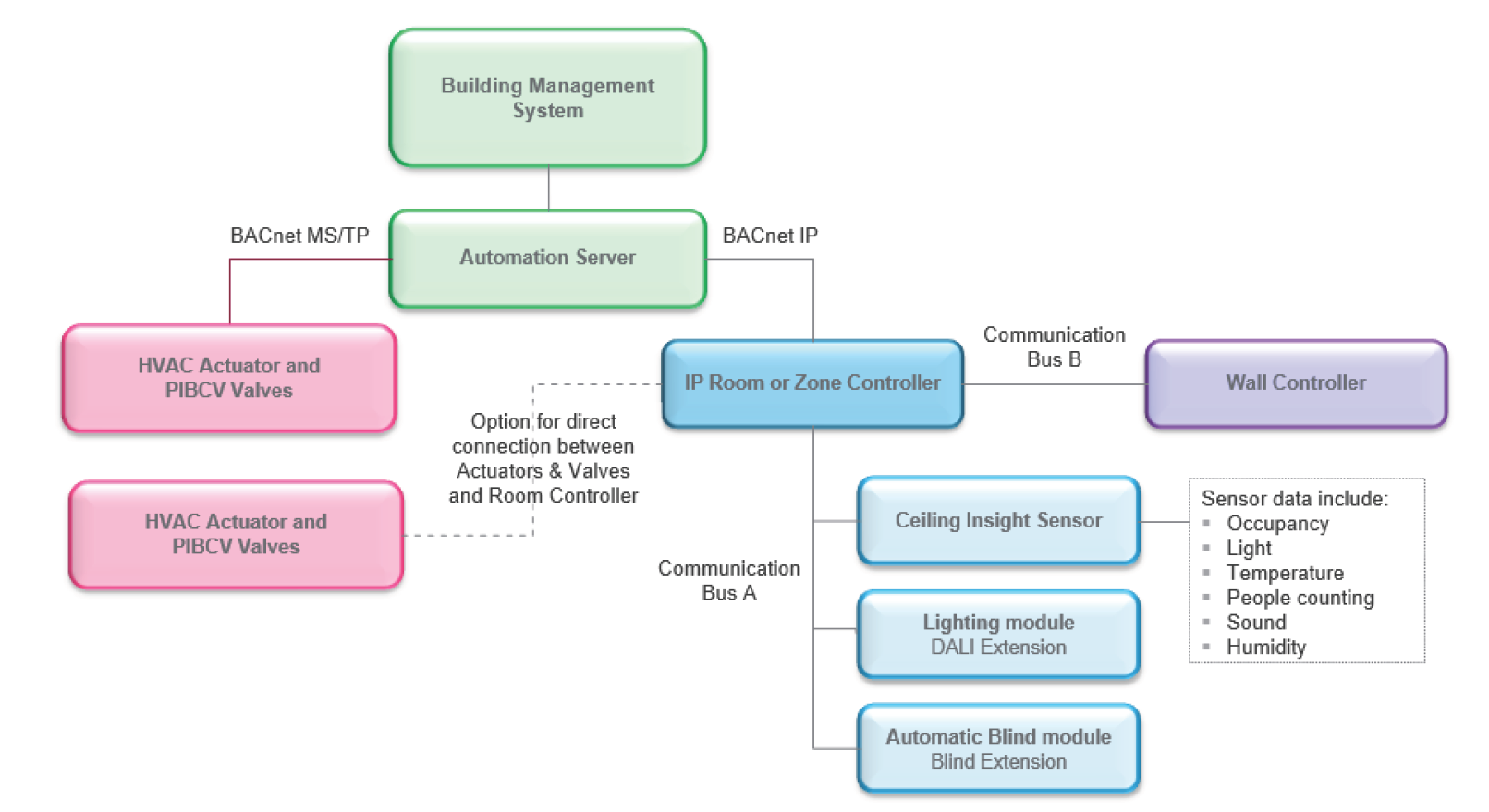
Insight sensors were positioned in the reception, café, open plan office, and meeting rooms. The intention was to foster a data-rich environment, support real-time control of the lighting and temperature, and enable occupants to identify and select zones for use based on the activities they need to carry out. Real-time occupant, noise, temperature, and humidity data could be mapped and viewed by building managers. More basic occupancy and temperature sensors were planned in the restrooms to control lighting and temperature only.
Like the traditional BMS control scenarios, the floorplan using modern BMS controls were planned with separate four pipe FCU’s for cost and embodied carbon comparison. The FCUs were connected to Pressure Independent Balancing and Control Valves (PIBCV) and differential pressure regulators to control and balance the flow and temperature of water supplied to each unit. To allow the valves and regulators to be controlled remotely, they were combined with PIBCV Actuators. The aim was to provide remote HVAC commissioning, flow balancing, and performance variation alarms. Each actuator was a daisy chain connected via the BACnet MS/TP Bus to the automation server. This was intended to allow control, energy demand monitoring, and the opportunity to utilize the smart analytics that are part of the modern BMS.
Financial assessment
Arup and Schneider Electric explored the difference in capital cost for the traditional BMS controls versus modern BMS controls. Arup developed a bill of quantities based on the design components and Schneider Electric added the unit price for each item.
Additionally, to understand any difference in time and cost of installing and commissioning the two systems, Schneider Electric made an informed cost estimate for electrical installation services for HVAC and lighting, as well as system commissioning.
Embodied carbon assessment
reduced by nearly half by 2030
reduced by nearly half by 2030
The World Resources Institute indicates that greenhouse gas (GHG) emissions need to be with the aim of achieving net-zero targets by 2050. Accordingly, the United Nations and a growing number of national and local government and business leaders are making commitments to reach net-zero emissions.
Phase 1: Findings and Key Takeaways
Table 1
Comparison of financial and embodied cost between Traditional BMS Controls and Modern BMS Controls with room-level capabilities.
embodied carbon emissions
embodied carbon emissions
To support these efforts, product manufacturers will need to calculate and publish for the whole product lifecycle. It includes the emissions from material extraction and processing, all manufacturing processes, all the fixtures and fittings, logistics, as well as deconstructing and disposal at the end of its useful life.
At the time of writing, measurement of the embodied carbon impact of building services installations is evolving rapidly, with significant variations in practice between markets. Bottom-up estimates of MEP embodied carbon, based on detailed bills of quantities are starting to be undertaken, but there is a significant lack of product level data to support this. This study carries out a detailed quantification of the embodied impact of a BMS installation, and this alone is significant progress compared to current practice.
At the time of this study, Schneider Electric calculated and published the Product Environmental Profiles (PEPs) that included embodied carbon (kgCO₂e) data for many of the products used in the study. This provided clear details on the environmental impact of the products used. If PEP information was not yet available for newer products such as the insight sensor, Arup’s Material Sustainability team developed an informed estimate of the embodied carbon impact, based on the available data for equivalent products with similar materials configuration.
For the scenarios modelled, the financial and embodied carbon assessment demonstrated that traditional BMS controls with FCUs are 18% less expensive to deploy than modern BMS controls, but the modern components have 23% less embodied carbon than the traditional controls configuration. See Table 1.
Traditional BMS Controls | Modern BMS with Room-level Controls | ||||
Financial Cost | Embodied Carbon kgCO2e | Financial Cost | % £ Cost Difference | Embodied Carbon kgCO2e | % kgCO2e Difference |
£75,042 | 9,524 | £88,347 | +18% | 7,718 | -23% |
For context, this is approximately 2% of the overall upfront embodied carbon impact of a newly constructed office building, or about 8% of the building services installation.
Key takeaways
The lower upfront financial cost of traditional BMS controls was considered a positive for organizations that seek basic HVAC control and lower costs. But the higher embodied carbon, reduction in environmental control, and lack of detailed and real-time building performance data were seen as shortcomings. Furthermore, the traditional controls and layout could prove less flexible with reconfiguration of space, thus proving potentially more costly in the long term.
Comparatively, modern BMS controls with room-level capabilities, lower embodied carbon, real-time data and insights and better control and optimization of the space, were seen as definitive positives. The combined sensor
Phase 2: Scope and Methodology for Operational Energy Performance
Figure 6
3D representation of the building geometry in IES
technology and application analytics allow building managers and occupants to better control lighting and temperature, understand people density and noise levels in different areas of the building, to support the ideal environment for different activities. The insight sensor also provides humidity, and post-occupancy data, offering additional ‘intelligence’ for the control of HVAC and/or natural ventilation.
Phase 2 of the study focused on the potential operational benefits of modern BMS controls versus traditional BMS controls in the same modelled office. These included energy efficiency and carbon impact, occupant well-being, and maintenance of the system over time.
Energy performance of the two systems was evaluated via a simulation using physics-based model of the building, and the following energy performance scenarios were identified for analysis and comparison:
- Air flow control
- Temperature set point control
- Auto blinds and daylight control
- ASHP (Air Source Heat Pump) flow temperature control
- Pump control
Energy Performance Modeling Setup
A three-dimensional model of the building was developed using Integrated Environmental Solutions Virtual Environment software (IES VE). This model captured various characteristics such as the thermal performance of the building fabric, air permeability, weather conditions and internal gains of the 945m2 building. The Chartered Institute of Buildings Services Engineers (CIBSE) weather files for the location in London were used. The floor plan layout was derived from Phase 1 of the study. The floor is glazed over two sides. The south and east facades have a proportion of glazing of 35% and 31.5% respectively, while the north and west are solid. Figure 6 is a 3D representation of the building geometry as setup in IES:
It was assumed that the building will be occupied 7 days a week from 7 a.m. – 7 p.m. An approximate number of occupants was assigned to each room depending on the activity in the space. A degree of randomness was added to each rooms’ occupancy profile to avoid the assumption of overlapping.
Lighting loads for each room were assigned following a luminaire layout assessment that was carried out in Phase 1. The floor plan was divided into 10 sections and different types of lamps were assigned across the floor. The luminaire power consumption and quantity were used to calculate the lighting load per room. Lighting profiles were set up following guidance from the National Australian Built Environment Rating System (NABERS) for office occupants’ lighting. NABERS is widely considered to be a world leading environmental performance rating tool for commercial buildings.
The baseline profile for lighting assumed a 5% ‘on’ status during out-of-work hours. During work hours of 8 a.m. to 5 p.m., lighting started ramping up until a 100% at 10 a.m. until close of business. It ramped down again going back to the default of 5% overnight. 15% of the lighting stayed on during work hours over the weekends.
Handbook for estimating NABERS ratings V2
Handbook for estimating NABERS ratings V2
Similarly, for equipment and small power loads for each room, power consumption figures were calculated using the . Small power density in watt per square meter was calculated per zone. A default 25% small power was set as running during out-of-work hours. During weekdays, equipment load was set from 65% at 8 a.m. to a 100% from 10 a.m. to 5 p.m. As for HVAC systems, the building was assumed to be fully mechanically ventilated and air-conditioned with defined specifications. Centralized balanced ventilation was assumed for the building provided by an Air Handing Unit with a specific Fan Power. Supply air temperature was set at 18 °C. Data for each variable was specified across humidity, primary and secondary heating, and cooling equipment.
Phase 2: Results and Key Takeaways of Energy Performance Scenarios
Once all the data was included in the model, the next step was to start modelling the energy consumption of the building for the baseline with traditional BMS controls, to make comparisons against the potential benefits of modern BMS controls. Sustainable building operations revolve around both monitoring and controls of an individual space. As noted previously, modern BMS controls allow for the integration of HVAC, lighting, blinds, and sensors for room environment monitoring supporting more dynamic, responsive, and demand-based actions. The following is a review of the energy performance scenario analysis:
Air flow control
This scenario suggested that having more occupancy-based airflow (and reducing volume of fresh air when spaces are unoccupied) could lead to significant energy savings. The use of occupancy sensing in combination with CO2 data provide accurate information about actual occupancy of space, allowing for zonal control of fresh air supply. However, this approach might require hardware changes or retrofits, specifically the availability or installation of Variable Air Volume (VAV) boxes per zone to facilitate local shut-off.
A ramp function was utilized in the model to modulate the air flow based on occupancy, with CO2 concentrations of less than 400 ppm indicating an unoccupied room and 1000 ppm representing a fully occupied room in need of full ventilation. To calculate air side fan power energy, an air flow to fan power curve was derived for the fan using peak rated air flow and Specific Fan Power (SPF) for peak fan power values. The traditional BMS controls scenario assumed that the fan would not turn down any lower than 60% independently of whether the room is occupied or not. Comparatively, in the modern BMS controls case, the fan will turn down (depending on zone occupation) to 0% if the zone or space is unoccupied.
The energy impact of this scenario is significant, as it shows that supplying air based on occupancy can reduce energy use by approximately of 15% HVAC +
Lighting energy savings, which translates into whole building EUI saving of 10% compared to a scenario when ventilation is provided regardless of occupancy. This reduction in energy consumption was achieved through the reduction of fan energy and heating and cooling energy associated with conditioning the air. In terms of carbon emissions, assuming an electricity carbon emission factor of 0.2 kgCO2/kWh this scenario would save approximately 1.9 tonnes (or 1,900 kg) of CO2 per year on the HVAC and lighting energy consumption.
Overall, this scenario highlighted the potential benefits of using occupancy sensing and CO2 data to control fresh air supply in buildings. While this approach requires a hardware change, the energy savings that can be achieved make it a compelling option for reducing energy consumption and associated costs. It is important to note that the assumptions made in this scenario may not hold true for all buildings.
Temperature Set point control
This scenario focused on the impact of broadening temperature set points on HVAC energy consumption when spaces were unoccupied. The objective was to reduce heating and cooling loads by increasing the temperature dead bands (e.g. range in which neither heating nor cooling turns on) using occupancy data from modern BMS controls. A heating setback of 16°C and cooling set back of 29°C was set for unoccupied spaces.
It was assumed that occupants would accept the temperature of the zone on reoccupation, which may not be as expected and will take time to return to the occupied set-point. The scenario also assumed that when rooms are unoccupied, the heating or cooling set point will go to a setback position.
To model the scenario, individual heating and cooling set point profiles were created for each room. The approach used was to assign a set of heating and cooling set point timings to each room, following the randomized occupation levels noted earlier.
The energy impact of broadening temperature set points was considerable, with a significant reduction in energy consumption observed. In this case, the biggest impact was seen in the reduction of room heating load, with an approximate energy demand reduction of 14% HVAC + Lighting energy savings, which translates into whole building EUI saving of 9%. Similarly, assuming an electricity carbon factor of 0.2 kgCO2/kWh this scenario would save approximately 1.8 tonnes (1,800 kg) of CO2 per year on the HVAC and lighting energy consumption.
It is important to consider the assumptions made in this scenario and evaluate the impact on occupant comfort and satisfaction. The impact of broadening temperature set points on energy consumption may also vary depending on the specific building and HVAC system being used, and accordingly, a detailed analysis would be necessary before implementing such control strategies.
Automatic Blinds and Daylight Control
This scenario assessed the integration of automated blinds as shading devices in the office building to study their impact on energy demand compared to traditional manual blinds. It focused on the effects of blinds on cooling, heating, and lighting. Different parameters related to the blind settings such as conditions to lower/tilt the slats, thermal resistance of blinds, shading coefficient, short-wave radiation fraction, etc., were evaluated. Some of the scenarios taken into consideration were:
- Baseline: no blinds
- Traditional controls scenario: manually lowered blinds
- Modern controls scenario: based on conditions such as irradiance and internal temperature.
The best iterations that consider both irradiation and internal temperature achieved a cooling demand reduction of 11% compared to the baseline and 7% compared to the traditional scenario, with a minimal increase in the heating demand. The impact on lighting demand with the best automated iteration achieves 3% increase in lighting demand compared to the baseline and 6% savings compared to the typical scenario. Combining the effect of automated blinds on all three parameters (internal temperature, internal daylight and lighting), the best iteration yields a reduction on 0.4% of the total building EUI.
Overall, in this specific case study building, automated blinds provided only marginal benefit compared to the traditional scenario, 1% HVAC + Lighting energy savings, which translates into whole building EUI saving of 0.4%. Considering the significant installation and maintenance costs, the benefits are negligible. However, different office layout with increased cooling dependencies may yield considerably different results.
Given the low energy savings on this scenario, carbon savings are negligible.
ASHP flow temperature
This scenario focused solely on zones with an Air Source Heat Pump (ASHP) and assessed the change in equipment efficiency when the chilled water supply temperature was elevated as demand was reduced. It used an Electronic Pressure Independent Control (EPIC) Valve, which provided direct feedback to the BMS confirming whether the energy demand of the FCU was being met at any point in time. The demand signal was used to reset the chilled water flow temperature, with the flow temperature raised to the point where all EPIC valves were just satisfied, providing much more direct demand feedback than looking at basic valve position or air temperature set-points.
The analysis assumed several conditions, such as a higher capacity ASHP being used due to the small room sensible cooling demand of the model, the ASHP providing chilled water to FCUs only, and the ASHP operating within 3 chilled water supply temperature control bands (6, 9, and 12°C). Three FCUs were selected to serve spaces, and a 14°C FCU off-air temperature was assumed.
The approach taken to calculate the operational energy savings of this scenario involves several steps, such as:
- Obtaining the cooling loads of each space throughout the year in 1-hour intervals using the modern BMS controls Phase 2 IES model
- Exporting outside air conditions
- Calculating the ASHP part-load capacity as a percentage rounded to the nearest 10% for each hour
- Sizing FCUs for each room using manufacturer data relating to FCU performance in each control band
- Calculating the highest chilled water supply temperature that can still meet the cooling demand of all spaces for each time interval
This drives the control band that the ASHP will operate in at that given time, with control band 1 (6°C chilled water supply) being used throughout the year for the baseline case. Finally, using ASHP manufacturer data, the Energy Efficiency Rating was determined for a given control band, outdoor
condition, and part-load capacity for each hour, obtaining the average of these values to determine the average change in ASHP efficiency throughout the year.
Elevating chilled water temperature when demand is reduced meant an increase in chiller efficiency of 8.8%. The increase in efficiency of the chiller would mean 1% HVAC + Lighting energy savings, and whole building EUI saving of 0.6%.
Given the low energy savings on this scenario, carbon savings are negligible.
Pump Control
This scenario described a comparison between traditional pump control using two-port Pressure Independent Control (PIC) valves with constant pressure set-point and a new method that used the EPIC valves providing direct flow measurements to the BMS. The study assessed the potential energy savings that could be achieved by operating the pumping system efficiently at part load. The focus was on the secondary circuit, and the analysis considers the impact of control on pump energy consumption.
The analysis showed that controlling pump power so that the differential pressure reduces to match the design differential pressure across the most distant sensor in the secondary system can achieve 9.5% HVAC + Lighting energy savings, which translates into whole building EUI saving of 6.4%. Assuming an electricity carbon factor of 0.2 kgCO2/kWh this scenario would save approximately 1.2 tonnes (1,200 kg) of CO2 per year on the HVAC and lighting energy consumption.
The study, however, assumed a typical pump specification and design pressure, which may not be representative of all pumping systems. The heating and cooling loads were extracted from the IES model to determine the system's flow rate, and the maximum cooling and heating flow rate requirements for the building were determined. The traditional BMS controls scenario assumes constant pressure control for the primary and secondary circuits independently of the flow rate across the pump. The results were specific to the secondary circuit. Nonetheless, this scenario provided a valuable starting point for designing efficient pumping systems that could lead to significant energy savings.
Key Takeaways from Phase 2
Although the scenarios and measures seemed to provide high energy savings when assessed individually, these energy saving measures would affect and have impact on each another when implemented together. Therefore, assessing the combination of all measures provided a more realistic figure of total energy savings and yielded an overall savings of 39% in HVAC and lighting electricity and an overall reduction of 26% in whole building EUI. An additional assessment estimates a combined carbon reduction by 7.88 tonnes (7,880 kg) of CO2 per year in calculations for the HVAC and lighting savings. See Figures 7 and 8.
Figure 7
Chart showing % energy savings when using modern BMS with room-level controls versus a traditional BMS control system.
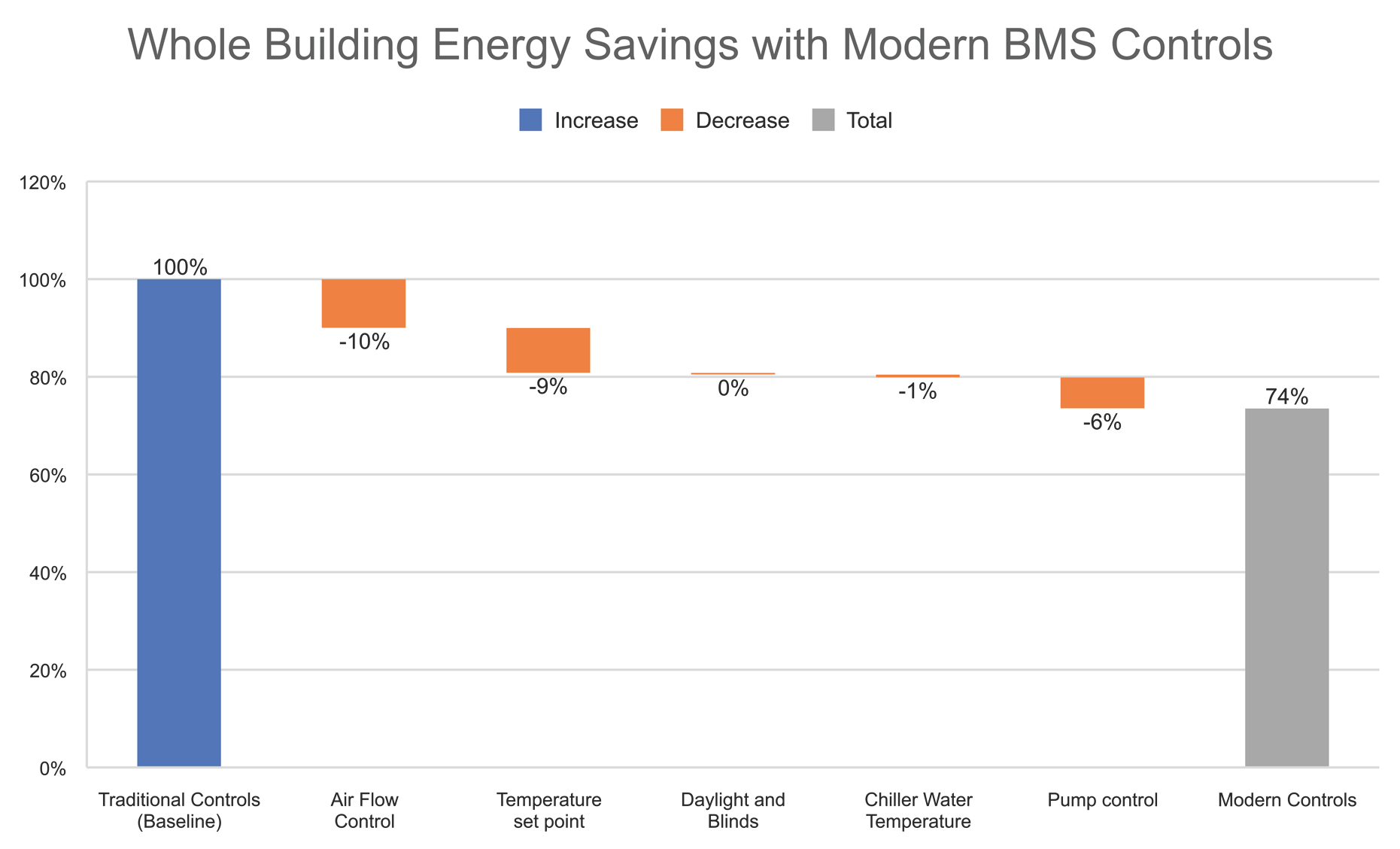
Figure 8
Chart showing reduction of carbon emissions related to HVAC and lighting when going from traditional BMS controls to a modern BMS with room-level controls.
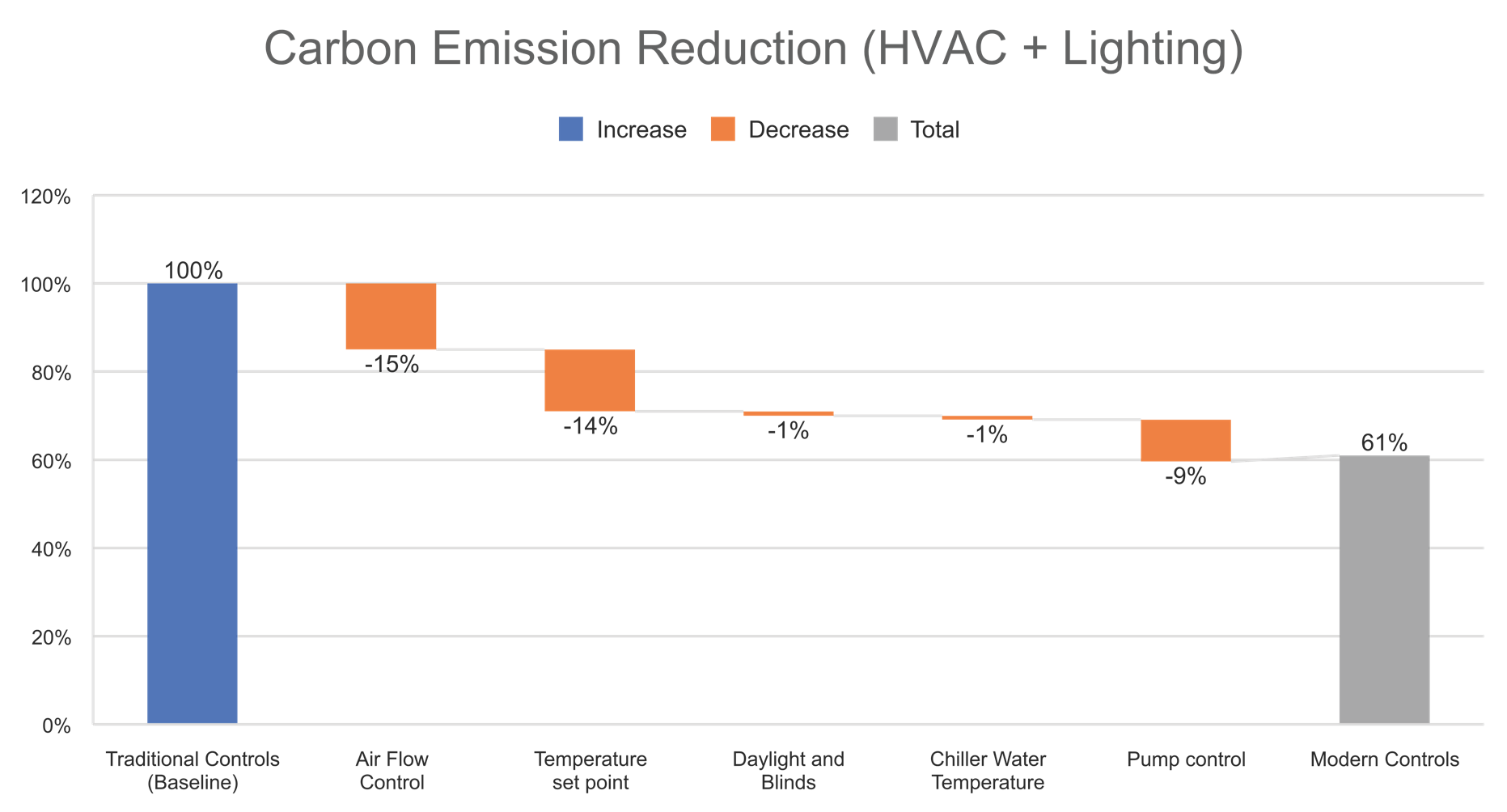
Conclusion
This paper provides a summary of a technical, theoretical case study performed by Arup in collaboration with Schneider Electric. Using Schneider Electric solutions in both scenarios, Arup’s study sought to compare and quantify the performance of two different types of building control design. The study was conducted in two phases:
Phase 1 – Capital project performance that assessed capital cost and embodied carbon of systems.
Phase 2 – Operational performance that assessed energy efficiency and operational carbon use.
The study demonstrated that the modern BMS controls with room-level capabilities offered up to 39% savings on HVAC + lighting and 26% overall whole building Energy Use Intensity. As well as 23% lower embodied carbon than traditional BMS controls, when deployed in a modelled new construction project. In addition, there were a host of other benefits associated with modern controls including easier system maintenance, better occupant experience and simpler reconfigurations of the building as changes occur over time.
Finally, Schneider Electric, independently of Arup, evaluated the ROI and potential payback period of the investment in the modern BMS controls infrastructure. The methodology included evaluating the higher capital cost of the modern system against the cost of energy saved due to operational benefits. Current pricing for electricity in London was used, both price per kWh for operational use as well as the standing electricity charges annually. Based on the energy saved, the payback period for the modern BMS controls system is approximately 1.7 years.
About the authors
Brook Potter of Schneider Electric is a Director of Sustainability in Schneider Electric’s Digital Buildings Division. His focus is on decarbonization of commercial buildings and ensuring that Schneider’s products deliver outcomes that drive saved and avoided carbon emissions. He brings over 15 years of experience leading product management for global software offers that help AECO professionals develop and operate commercial buildings that are more sustainable, achieve higher operating potential, and deliver transformative experiences for occupants.
-
-
Anubama Chinnakannan of Schneider Electric is an Application Engineer in Schneider Electric's Digital Buildings CTO office. Her focus is on Energy Systems engineering, BMS solutions for building segments, data experimentation, semantic tagging, and evaluations of startups in the buildings domain. She also works on multi-technologies research and innovation in the field of grid-interactive buildings, commercial sensor technologies, and AI for HVAC optimization, among other areas. She is a WELL Accredited Professional, LEED Green Associate and Certified CESAM Associate.
-
-
Stephen Hill of Arup is an Associate Director and sustainability consultant with 25 years’ experience. He specializes in the development of carbon and sustainability strategies for buildings and portfolios across a range of sectors. Stephen is passionate about the climate crisis and whether working on an individual building or across industry is a strong advocate for the property sector’s transition to Net Zero. He is a member of the NABERS UK Independent Design Review panel and is Arup’s representative on the BCO ESG Committee. He was also the CIBSE Building Performance Engineer of the Year 2023.
-
Carolyn Caceres of Arup is an enthusiastic engineer with 15 plus years of experience in the field of energy and sustainability in the built environment. Her expertise includes using and developing energy models for new and refurbishment building projects and using dynamic simulation modelling tools to calculate energy consumption and associated carbon emissions. She has wide knowledge of the built environment and the challenges it faces in relation to climate change, with solid background in passive design and zero carbon building principles.
© 2023 Schneider Electric. All rights reserved.