Case Study: Do Green Buildings Perform as Designed?
This case study seeks to determine if the green technologies used within a LEED-certified building are performing as designed, assessing the operational performance of the technology and strategies for water/energy usage relative to design parameters.
Do Green Buildings Perform as Designed: A Case Study of the First LEEDNC Gold Certified Building at RIT?
Jeffery Rogers1 and Sultan Alraddadi2
Abstract
Numerous buildings that are designed under the USGBC’s LEEDNC certification framework have been in operation for at least five-years. In order for this building to be continued to be recognized as a green building it must meet the USGB’s LEEDEB re-certification framework. Therefore, it is reasonable facility managers to ask if green buildings are performing as designed. The goal of this case study is to determine if the green technologies and strategies designed within a LEEDNC certified or green building are performing as designed. The objectives of this case study are to assess the operational performance of the green technologies and strategies for: (1) water and (2) energy usages relative to design parameters. The expected outcome of this case study is a methodology for facility managers to assess the operational performance of the green technologies and strategies. The results of this case study were inconclusive regarding the assessment of the levels of performance of the green technologies and strategies for water and energy usages. It was impossible to assess the actual vs. design green water and energy systems performance without adequate metering data representing the outputs from the green technologies and strategies over the five-year operational period.
Keywords: Green Building, Green Technologies and Strategies, LEED, Water & Energy Usage
Introduction
Over the past decade thousands of buildings have been designed and built incorporating multiple green technologies and strategies (Mills et al., 2012). The green building movement has essentially changed the built environment by designing cost-effective and resource-efficient buildings that enable sustainable economic, social, and environmental impacts on global environment (Silverman & Mydin, 2014; Sichelman, 1999). For example, Kriss (2013) reports there are approximately 60,000 LEED building projects spanning 10.6 billion square feet in more than 140 countries around the world. Additionally, the Environmental Leader (2010) predicts that the market value of green technologies and strategies within the US green building sector will increase from $150 billion to $173 billion by 2015.
Numerous buildings that are designed under the USGBC’s LEEDNC certification framework have been in operation for at least five-years. In order for this building to be continued to be recognized as a green building it must meet the USGB’s LEEDEB re-certification framework (USGBC, 2014). Therefore, it is reasonable facility managers to ask if green buildings are performing as designed under the USGBC’s LEEDNC certification framework. Additionally, is it
cost-effective to re-certify under the USGB’s LEEDEB certification framework an existing green building. The goal of this case study is to determine if the green technologies and strategies designed within a LEEDNC certified or green building are performing as designed. The objectives of this case study are to assess the operational performance of the green technologies and strategies for: (1) water and (2) energy usages relative to design parameters. Essentially, this case study provides a methodology for facility managers to assess whether to re-certify a LEEDNC certified building as a LEEDEB certified building. This case study is significant because the cost for preparing the documentation for the: (1) LEEDNC certification application can approach approximately 0.55% of a project’s total design and construction cost (RIT, FMS, 2008) and (2) LEEDEB re-certification application can approach approximately $0.10 per square foot depending on a facility’s overall square footage (USGBC,2014).
The case study first presents essential background information on the green building and then discusses the relevant green technologies and strategies for reducing overall water and energy usage. Next, the case study covers the methodology utilized for analyzing the five-year operational data from the relevant green technologies and strategies. Then, the case study presents the operational performance results for the green technologies and strategies as compared to relevant design parameters. Finally, the case study concludes with relevant recommendations, lessons learned, and future work activities.
Background
This case study involves an analysis of the operational performance of the first green certified building on the RIT campus. In 2008, the CAST (College of Applied Science and Technology) building achieved its LEEDNC Gold certification (RIT, FMS, 2008). The CAST building consists of three floors spread over 42,956 ft2 (3,991 m 2). The space planning consists of multi-use laboratory, lecture, conference, and office spaces, as shown in Figure 1:
Source: (RIT, FMS, 2008)
Figure 1. Pictorial of the CAST building on the RIT campus
Figure 1 shows the basic layout and orientation of the CAST building on the RIT campus. The document preparation fees for LEED certification was approximately $59,500 (RIT, FMS, 2008). The capital costs for the design and construction of the associated green feature technologies and strategies for the CAST building were approximately $157,500 (RIT, FMS, 2008). Finally, the associated operational saving over a 20-year evaluation period for this green building design was estimated to be approximately $25,000 per year or total of $500,000 (RIT,
FMS, 2008). This case study analyzes the actual performance of the CAST building’s green technologies and strategies for water and energy usage over its 5-year operational period.
Green building occupancy
This case study assumes that the CAST building’s occupancy remains relatively constant during the university’s academic calendar. The CAST building was initially designed to accommodate 233 (41 faculty/staff & 192 students/visitors) full-time equivalent (FTE), as detailed in Table 1:
Table 1. Occupancy Escalation and Expected Green Water and Energy Usage Impacts
Annual Usage | FY09 | FY10 | FY11 | FY12 | FY13 |
Beginning FTE Occupancy | 233 | 233 | 241 | 250 | 259 |
Student Escalation | 0 | 8 | 9 | 9 | 9 |
Ending FTE Occupancy | 233 | 241 | 250 | 259 | 268 |
Total Green Water Usage (gallon/yr) | 22,500 | 23,275 | 24,140 | 25,000 | 25,875 |
(liter/yr) | 85,172 | 88,106 | 91,380 | 94,635 | 97,948 |
Total Green Energy Usage (KWh/yr) | 992,500 | 1,026,575 | 1,064,915 | 1,103,250 | 1,141,590 |
Note: Student escalation is based on university enrollment numbers for academic programs within CAST building.
Table 1 reveals that the number of students, i.e. verified through increasing enrollment numbers, has escalated by 35 FTE over the CAST building’s operational period. The number of faculty, staff, and visitors remained relatively constant over this same period. Table 1 also reveals that the expected escalation impacts on the CAST building’s green water and energy usage are approximately 96.5 gallons (365.3 liters) per year per FTE and 4,260 KWh per year per FTE, respectively.
Green building water and energy systems
The CAST building’s water and energy systems were designed with green technologies and strategies that are expected to reduce typical: (1) water use by 70% and (2) energy use by 40%. If these design parameters are met than the CAST building is expected to consume: (1) 22,500 gallons (85,172 liters) water per year and (2) 992,500 KWh of energy per year. The following sections provide a detailed description of the green water and energy systems of the CAST building.
Green water system
The CAST building’s water system was designed as a dual-distribution system that involves isolated drinking and non-drinking water piping systems. The potable water piping entering the CAST building is metered. However, within the CAST building neither the drinking water loop nor non-drinking water loop is metered. This finding is significant because it is impossible to determine how much of the metered potable water entering the building is consumed as either drinking or non-drinking water. The non-drinking water is used to supply the CAST building’s urinals and water closets.
Historically, a laboratory/academic building such as the CAST building would be designed to consume approximately 75,500 gallons (285,790 liters) per year. However, by utilizing various green technologies and strategies the CAST building was designed to save approximately 70% or 53,000 gallons (200,620 liters) of water per year when compared to a typical laboratory/academic building, as detailed in Table 2:
Table 2. CAST Building’s Non-Drinking Water Usage Expected Savings
Green Technologies and Strategies | Water Savings gallon/yr liter/yr | Avg. Unit Cost $/1000 gallon | Avg. Savings $/year |
Rainwater collection system for non-drinking water | 36,000 136,275 | $ 3.29 | $ 118 |
Low-flow water devices such as urinals & closets | 8,500 32,176 | $ 28 | |
Drought-tolerant regional landscaping | 8,500 32,176 | $ 28 | |
Total Non-Drinking Water Usage Savings | 53,000 200,627 | $175 |
Source :( RIT, FMS, 2008; Water Utility: http://ecode360.com/8674019?#8674019 )
Table 2 reveals the implemented green technologies and strategies with expected non-drinking water savings that are designed into the CAST building. The implemented green technologies and strategies include: (1) rainwater collection system (RCS); (2) low-flow water devices such as urinals and water closets; and (3) drought-tolerant regional landscaping strategies. Therefore, given the above green non-drinking technologies and strategies and design 233 FTE occupancy for the CAST building, the expected green water usage is designed to be approximately 22,500 gallons (85,172 liters) per year.
The most significant green technology is the non-drinking water contribution or savings from the RCS. The RCS was designed to divert rainwater from the roof of the CAST building into two 1,500-gal rainwater storage tanks located within basement, as shown in Figure 2:
Figure 2. Schematic Diagram for the Rainwater Collection System of the CAST Building
Figure 2 shows a piping diagram for the RCS, which contributes rainwater to the non-drinking water loop. Any over-flow rainwater volumes are piped to the exterior of the building when the tanks are full. The design output capacity of the RCS is 36,000 gallons (136,275 liters) per year. A significant finding was that the existing 2-inch meter for the RCS had not worked throughout the entire operational period. Without adequate metering to collect operational data on the water system within the CAST building it was impossible to accurately determine the level of performance of the green technologies and strategies for the water system.
Green energy system
The CAST buildings energy system was designed to utilize electrical energy from the local utility for normal electrical loads. The CAST building’s heating and cooling energy is managed within the university’s central plant, i.e. hot and cold water loops. The CAST building’s electrical service is metered, while the heating and cooling usage is not metered. This finding is significant because it is impossible to determine how much of the un-metered heating and cooling usage contributes to the CAST building’s overall energy usage.
Historically, a laboratory/academic building such as the CAST building would be designed to consume approximately 1,648 KWh (5,621MBtu) of energy per year. However, by utilizing various green technologies and strategies the CAST building was designed to save approximately 40% or 656,100 KWh (2,238MBtu) of energy per year when compared to a typical laboratory/academic building, as detailed in Table 3:
Table 3. CAST Building’s Energy Usage Expected Savings
Green Technologies and Strategies | Energy Savings KWh per yr | Avg. Unit Cost $/KWh | Avg. Savings $/year |
Solar Collection System for electrical load | 2,700 | $0.089 | $ 245 |
Other energy conservation features | 655,400 | $ 58,155 | |
Total Energy Usage Savings | 656,100 | $ 58,400 |
Sources: (RIT, FMS, 2008; Electric Utility: http://www.rge.com/SuppliersAndPartners/pricingandtariffs/default.html )
Table 3 reveals the implemented green technologies and strategies with expected energy savings that are designed into the CAST building. The implemented green technologies and strategies include: (1) solar collection system (SCS); (2) air barriers in building envelope; (3) HVAC controls that monitor building occupancy; and (4) natural and passive lighting strategies. Therefore, given the above green energy technologies and strategies and design 233 FTE occupancy for the CAST building, the expected green energy usage is designed to be approximately 992,500 KWh (3,384MBtu) of energy per year.
The most significant green technology is the electrical energy contribution or savings from the Solar Collection System (SCS). The SCS was designed to convert solar energy into electrical energy via an auxiliary AC/DC inverter system, as shown in Figure 3:
Figure 3. Schematic Diagram for the Solar Collection System of the CAST Building
Figure 3 shows the SCS’s twelve polycrystalline-silicon solar panels were located on the roof of CAST Building. The design output capacity of each panel is 2.25 KW per hour operated for a total of 27 KW per hour operated. A significant finding was that the existing meter for the SCS had not worked throughout the most of the operational period. Without adequate metering to collect operational data on the energy system within the CAST building it was impossible to accurately determine the level of performance of the green technologies and strategies for the energy system. In addition, the SCS was deactivated for several months due to deficiencies with the inverter.
This case study attempted to analyze the actual level of performance of the implemented green technologies and strategies for the water and energy systems within the CAST building. While it was apparent that critical water and energy consumption data was not available due to inadequate metering the following methodology presents relevant design formulas that can assist with the quantification of the non-metered or missing data from the RCS and SCS, respectively.
Methodology
The methodology of this case study includes: (1) quantitative analysis utilizing collected operational data or (2) design equation analysis utilizing relevant historic parameters. The methodology provides a procedure for facility mangers to follow in order to compare actual operational performance with relevant green design parameters. The purpose of this methodology is to provide a usable procedure for making green operational decisions. The proposed procedure also assists facility managers in handling situations when relevant operational data is missing. The proposed procedure recognizes the importance of relevant design equations for obtaining representative operational values when assessing actual performance. The beginning steps of the proposed procedure are to collect all of the relevant operational data and then compare this data with relevant design parameters to assess an associated level of performance. However, if relevant operational data is not available, then the proposed procedure utilizes relevant design equations and historical data to estimate the operational data. The steps of the proposed procedure are detailed in Table 4.
Table 4. Steps for the Proposed Procedure to Assess Operational Performance
No. | Steps | Tasks | Expected Outcomes |
1 | Data Identification | Understand building systems Meet with relevant employees Research relevant resources | Synthesis data & resource needs |
2 | Data Collection | Gather building operational data Gather relevant historical data | Collect metered data Identify missing data |
3 | Database Construction | Generate databases Describe data & process Determine data relationships | Construct water & energy database |
4 | Data Transformation | Identify consistent unit conversion Validate parameter assumptions | Transform data |
5 | Data Analysis | Assess available metered data Perform calculations on non-metered data Draw charts to understand data characteristics Document abnormal and extreme data | Assess metered data Assess missing data |
6 | Data Results | Calculate performance Identify future improvements | Design vs. actual System improvements |
Table 4 reveals six general steps for identifying, monitoring, gathering, and analyzing data. It is important to note that each application of this procedure is unique regarding the overall database construction. Additionally, note the tasks and outcomes are different for metered and non-metered operational data.
Metered operational data for the CAST building
The CAST building’s potable water meter quantifies the actual potable water used over a given period. The metered value represents the total amount of drinking and non-drinking water consumed over a given period. However, once the potable water enters the building water system there is no metering to quantify the amount of: (1) drinking water consumed or (2) rainwater contributed to the non-drinking water volume by the RCS. Therefore, the level of performance of the RCS cannot be quantified.
The CAST building’s electric meter quantifies the actual electrical energy used over a given period. The metered value represents the total amount of electrical energy consumed over a given period. However, once the electrical energy enters the building energy system there is no metering to quantify the amount of: (1) heating and cooling energy consumed or (2) solar energy contributed to the energy volume by the SCS. Therefore, the level of performance of the SCS cannot be quantified.
Non-metered operational data for the CAST building
A reasonable estimate for the level of performance of the RCS may be calculated by inputting relevant parameters into equation 1:
(1)
Where:
Q= Collected rainwater, gallon (liter) per month
R= Precipitation, inch (mm) per month
2
2
A= Footprint of collection surface, ft (m)
k= Unit Conversion factor
e= Efficiency of collection surface
Equation 1 is a general design equation for estimating the amount of rainwater collected from rooftops. Therefore, since the RCS’s contribution to the non-drinking water usage is non-metered equation 1 can used to estimate the level of performance of the RCS. For example, the CAST building’s RCS parameters are:
R= | historical precipitation data for Rochester, NY, inch per month |
A= | 12,693 ft 2 (m2) |
k= | 7.48 gal/ft3 ; 12 in/ft; and 12 months/yr |
e= | 0.90 |
Table 5 shows a summary of the calculations from the application of equation 1 to determine the level of performance or RCS efficiency over the CAST building’s operational period:
Table 5. RCS Level of Performance or Efficiency When Applying Equation 1
Year | Total R value in/yr mm/yr | Total Q value gallon/yr liter/yr | Design RCS Input gallon/yr liter/yr | RCS Efficiency | Meter Potable Water gallon/yr liter/yr |
FY09 | 36 914 | 264,400 1,000,825 | 36,000 136,275 | 13.6% | 59,685 225,932 |
FY10 | 32 813 | 232,500 879,940 | 36,000 136,275 | 15.5% | 115,246 436,254 |
FY11 | 40 1,016 | 291,000 1,101,520 | 36,000 136,275 | 12.4% | 23,762 89,949 |
FY12 | 36 914 | 266,400 1,008,300 | 36,000 136,275 | 13.5% | 180,195 682,112 |
FY13 | 37 940 | 271,300 1,027,105 | 36,000 136,275 | 13.3% | 142,251 538,479 |
Note: Average RCS efficiency is 13.7%
Table 5 suggests that if the RCS efficiency is assumed to be content, i.e. 13.7%, throughout the operating period then a high rainfall year such as FY11 should contribute significantly more rainwater for non-drinking water usage, which in turn suggests that the FY11 potable water reading should be significantly lower.
A reasonable estimate for the level of performance of the SCS may be calculated by inputting relevant parameters into equation 2:
(2)
Where:
E = collected solar energy, KWh/day
p
E= peak power of solar panel, KW
i = daylight hours, hours/year
n = number of solar panels
c = cloud cover efficiency factor
Equation 2 is a general design equation for estimating the amount of solar energy collected from rooftops. Therefore, since the SCS’s contribution to the electrical usage is non-metered equation 2 can used to estimate the level of performance of the SCS. For example, the CAST building’s SCS parameters are:
Ep = 0.185 KW, peak power of solar panel
i = historical daylight hours of Rochester, NY, hours/day
n =12 solar panels
Table 6 shows a summary of the calculations from the application of equation 2 to determine the level of performance or SCS efficiency over the CAST building’s operational period:
Table 6. SCS Level of Performance or Efficiency When Applying Equation 2
Operational Year | Total i value hrs/yr | Efficiency Factor, c | Total E value kWh/yr | Meter SCS KWh/yr | SCS Efficiency | Meter Electric KWh/yr |
FY09 | 4,442 | 0.94 | 9,281 | N/A | N/A | 519,097 |
FY10 | 4,437 | 1.06 | 10,430 | 930 | 8.9% | 765,451 |
FY11 | 4,458 | 0.82 | 8,150 | 1,708 | 21.0% | 1,118,905 |
FY12 | 4,479 | 0.94 | 9,358 | 1,367 | 14.6% | 1,603,886 |
FY13 | 4,446 | 0.91 | 8,999 | N/A | N/A | 1,195,863 |
Note: Solar energy is based on yearly average of 12 daylight hrs/day without considering cloud cover effect.
Table 6 shows the impact of the amount of daylight hours (i) and cloud cover (c) on the collected solar energy (E). For example, FY10 has the highest amount of collected solar energy due to the higher than normal amount of cloud cover. Table 6 also shows that metered SCS data is not reliable since its meter was not working in FY09 and FY13. Finally, Table 6 reveals that while there is a significant amount of collected solar energy available, the design capacity of the SCS has a minimum contribution to the electrical demand of the CAST Building.
Results
The green building’s actual cost savings from the increased operational efficiencies of the implemented green technologies and strategies could not be assessed relative to its intended design performance. The results of the case study compared the design water performance with the actual water usage performance over the 5-year operational period, as shown in Table 7:
Table 7. Results of the CAST Building’s Five-Year Operational Water Usage Analysis
Operational Year | Typical Water Usage gallon/yr liter/yr | Design WCD Savings gallon/yr liter/yr | Design RCS Savings gallon/yr liter/yr | Design Water Usage gallon/yr liter/yr | Metered Water Usage gallon/yr liter/yr | Actual Rainfall in/yr mm/yr |
Design | 75,500 285,800 | 17,000 64,352 | 36,000 136,275 | 22,500 85,170 | ||
FY 2009 | 59,685 225,932 | 36 914 | ||||
FY 2010 | 115,246 436,254 | 32 813 | ||||
FY 2011 | 23,762 89,949 | 40 1016 | ||||
FY 2012 | 180,195 682,112 | 36 914 | ||||
FY 2013 | 142,251 538,479 | 37 940 |
Table 7 shows significant inconsistencies between the design and metered (actual) water usages. Since the RCS output was not metered this research was unable to verify these inconsistencies. A recommendation is that the RCS output be metered. Table 7 also shows inconsistent metered water usage data. For example, FY2011 shows an extremely low reading, which could not be explained. Finally, Table 7 reveals that this research was unable to determine a direct
relationship between metered water usage and annual rainfall. Since the RCS output was not metered its overall contribution to the metered water usage could not be adequately explained. For example, since the long-term rainfall average is 34 inches per year the years in which this amount is exceeded should correlate to lower metered water usage readings. However, the data does not reflect this correlation. Overall, the research of the performance of the green technologies and strategies for water usage of the CAST Building was inconclusive.
The results of the case study compared the design energy performance with the actual energy performance over the 5-year operation period, as shown in Table 8:
Table 8. Results of the CAST Building’s Five-Year Operational Energy Usage Analysis
Operational Year | Typical Energy Usage KWh/yr | Design ECD Savings KWh/yr | Design SCS Savings KWh/yr | Design Energy Usage KWh/yr | Metered Electrical Usage KWh/yr | Total Daylight Hours, hrs/yr |
Design | 1,648,623 | 656,106 | 2,317 | 992,517 | ||
FY 2009 | 519,097 | 4,442 | ||||
FY 2010 | 765,451 | 4,437 | ||||
FY 2011 | 1,118,905 | 4,458 | ||||
FY 2012 | 1,603,886 | 4,479 | ||||
FY 2013 | 1,195,863 | 4,446 |
Note: ECD savings is represented as heating and cooling energy savings within hot and chilled water system
Table 8 shows significant inconsistencies between the design and metered (actual) electrical energy usages. Since the SCS output meter was not working properly throughout the 5 year operational period this research was unable to verify these inconsistencies. A recommendation is that the SCS output meter be repaired. Table 8 also shows inconsistent metered electrical energy usage data. For example, FY2012 shows an extremely high reading, which could not be explained. Finally, Table 8 reveals that this research was unable to determine a direct relationship between metered electrical energy usage and annual daylight hours. Since the SCS output was not properly metered its overall contribution to the metered electrical energy usage could not be adequately explained over the 5 year operational period. For example, if the longterm average daylight hours is 4450 hours per year the years in which this amount is exceeded should correlate to lower metered electrical energy usage readings. However, the data does not reflect this correlation. Overall, the research of the performance of the green technologies and strategies for electrical energy usage of the CAST Building was inconclusive.
The expected outcome of this case study is a methodology for facility managers to assess the operational performance of the green technologies and strategies within a LEEDNC building, especially when considering whether to seek re-certification as an LEEDEB a building. The results of this case study were inconclusive regarding the assessment of the levels of performance of the green technologies and strategies for water and energy usages. It was impossible to assess the actual vs. design green water and energy systems performance without adequate consumptive metering data representing the outputs from the green technologies and
strategies over the five-year operational period. The results of this case study are significant because facility managers are informed of the importance of continually measuring and monitoring the operational performance of implemented green technologies and strategies throughout the life-cycle of a green building.
Conclusions
The objectives of this case study were not met because to the assessment of the operational performance of the green technologies and strategies for (1) water and (2) energy usages could not be accurately measured relative to the intent of the green building’s design parameters. Therefore, the goal of this case study to determine if the green technologies and strategies designed within a LEEDNC certified or green building performed as designed was not met. Overall, the results of this case study were inconclusive due to missing and/or malfunctioning consumptive meters.
Without relevant operational data from consumptive meters over the entire five-year operational period it is impossible to accurately assess the levels of performance of the green technologies and strategies that are designed within green buildings. The recommendations of the case study are to: (1) install a new consumptive water meter at the point where the treated rainwater from the RCS enters the water distribution system; (2) install another consumptive water meter at the point where the potable water enters to the drinking water loop; and (3) repair the consumptive meter to measure the SCS electrical output; (4) install new consumptive meters in the hot and chill water loops to accurately measure heating and cooling energy usage. Finally, it is recommended that these water and energy meters be connected to the building’s energy management system in order to facilitate the green data collection process.
The lessons learned from this case study are the importance of installing adequate consumptive meters in order to determine the levels of performance of green technologies and strategies within green buildings. The accurate consumptive metering of operational data is essential in order to assess green building performance. Collecting, monitoring, and analyzing data from green technologies and strategies within green buildings will assist facility managers with determining the feasibility of continuing green building certifications.
The future activities for the continuation of this case study include implementing improved consumptive metering for green technologies and strategies to accurately assess the levels of the performance of the water and energy systems.
Acknowledgments
We would like to express our thank to the Director, Engineering Services and Manager, HVAC System Support from the RIT Facility Management Services, whom provided valuable insights during our data collection process for this case study.
References
Environmental Leader. (2010, July). “ Green Building Market to Hit $173.5 Billion by 2015ˮ, EL Insights, (Feb 24, 2014)
Kriss, J. (2013, November). “Nearly 60,000 Global LEED Green Building Projects Span 10.6 Billion Square Feet: New Report from USGBC with Introduction from Boston Mayor Meninoˮ, USGBC, (Feb. 24, 2014)
Mills, F., Lawrence, T., Rakheja, A., & Darwiche, A. (2012). “Green building practices around the worldˮ. ASHRAE Journal, 54(1), 48-52, 54-55. (Aug17, 2014)
Rochester Institute of Technology (RIT) Facility Management Services (FMS). (2008, June). CAST Project: A Case Study of the College of Applied Science and Technology (CAST) Building at RIT, (Feb 24, 2014)
Sichelman, L. (1999). “ 'Green building' movement getting a boost ˮ. Origination News, ABI/Inform Complete via ProQuest, 8(10), 6-6, 49.
Silverman, N., & Mydin, M. A. O. (2014). “Green Technologies for Sustainable Building ˮ. Acta Technica Corviniensis -Bulletin of Engineering, 7(3), 87-94. (Aug17, 2014)
United States Green Building Council. (2014). “LEED Certification.” Registration and Certification Fees, Building Operations and Maintenance Fees, (Aug17, 2014)
Want even more Content?
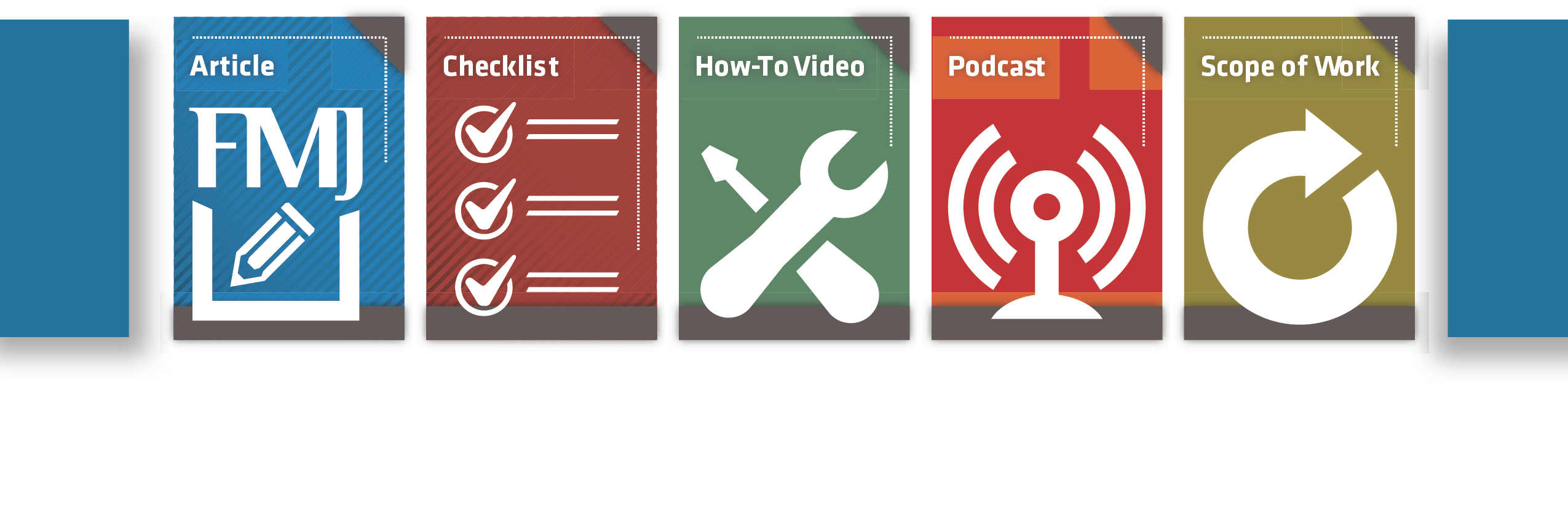
Since you’re already a user, you know that IFMA’s Knowledge Library offers all FM content in one place. But did you also know that by signing up via email to become a registered user, you can unlock even more resources?
Signing up via email for registered access within the Knowledge Library brings more content and functionality to your fingertips. Expect to grow your facility management knowledge, career and network faster than ever before.